By Karen Di Piazza
Peter Maurer, the North American president for Diamond Aircraft Industries, Inc., in London, Ontario, Canada, wants to set the record straight: “Diamond’s Canadian-based facility is equal to its Austrian-based sister.”
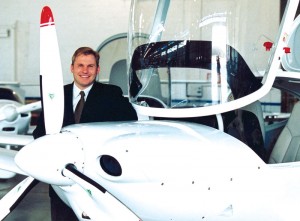
Peter Maurer, the North American president of Diamond Aircraft Industries, Inc., says they expect to hire more employees in the near future.
“Both are production facilities; the one located in Wiener Neustadt, Austria, is where headquarters are located, but they aren’t our parent company,” said Maurer, who is responsible for all R&D, manufacturing and operations for Canada and the U.S. “We equally share in workload and production.”
Maurer oversees about 250 employees at its quarter-of-a-million-square-foot facility in Canada.
“We expect to hire about 25 more employees, and about 350 people are employed in Austria,” he said.
He said both facilities work in tandem, creating an innovative aircraft solution that supports its major offices and centers across North America, Europe, Japan, England, South Africa and Australia.
Diamond has been around since 1981, when it was known as HOAC. Maurer joined the company in 1993. Before becoming president in 2000, he had been responsible for quality assurance and airworthiness, was chief engineer for three years and later became responsible for all operations.
“We are the type certificate holder for the four-seat, single-engine DA40, and the two-seat, single-engine DA20,” he said.
Embry-Riddle Aeronautical University plans to train 500 Air Force cadets annually at the Air Force Academy in Colorado Springs, Colo., using Diamond’s military version, the DA20-C1. The DA20 has been a popular choice for Canada’s flight schools, many of which still teach spin/stall training. Maurer said the DA20, priced at $125,000 for the basic aircraft, doesn’t include a glass cockpit option.
“We’re just at the beginning of the all-glass cockpit age, really,” he said. “There will be development in the future that will bring it to this class of aircraft as well.”
The DA40 starts at $190,000, but would jump to $260,000 with an all-glass cockpit.
The DA42 Twin Star
Maurer said you get a lot for your money with Diamond’s DA42 Twin Star, a twin diesel-powered aircraft priced at $439,000, which is “very well equipped with a Garmin G-1000 all-glass cockpit, autopilot and a premium leather interior.” It’s also a very efficient plane.
In mid-August, for the first time, a diesel-powered aircraft flew nonstop across the Atlantic, when a Diamond test pilot ferried the Oshkosh display DA42 back to the Austrian facility. First, in a 1,300-nautical-mile flight, which took only 7.5 hours, the DA42 made it from London, Ontario, Canada to Porto, Portugal, with only one stop, which was in St. John’s Newfoundland, Canada. From there, the DA42 crossed the Atlantic Ocean on its final 1,900-nm leg, flying nonstop for 12.5 hours.
Diamond said if it had not been for adverse weather conditions in Europe, the remaining five hours of fuel upon landing in Porto would have been sufficient to reach the planned destination of Toulouse, France, a nonstop distance of over 2,500 nm. The total amount of jet fuel consumed for the crossing, 72 gallons, cost less than $200!
Maurer said the point-to-point travel time was considerably faster than any available commercial flight combination, illustrating the Twin Star’s practicality, efficiency and reliability as a personal or business transportation alternative.
Out in the middle of nowhere trying to fix a composite plane
Although Diamond’s expertise in advanced composite technology dates back over two decades, and they have developed products for aerospace and defense applications that are in use worldwide, the average pilot questions the use of composites. Maurer answers this question: If you were out in the middle of nowhere, and you had damage to the airframe, what would happen?
“It’s true; there’s some trepidation on the part of pilots and technicians when it comes to composite structural repairs—due to their familiarity and comfort with repair of sheet metal structures,” he said. “In most cases, it’s basically just a fear of the unknown. In fact, the composite structures are less prone to typical hangar-rash type damage and are also more resistant to fatigue, which is currently a problem for aging metal aircraft, and tend to have more localized damage than metal aircraft.
“Additionally, a properly designed composite structure will offer far better impact protection for the occupants, versus a conventional sheet metal aircraft. Diamond uses an easily repaired low temperature curing epoxy system, which has definite advantages over higher temp curing prepreg systems when it comes to in-field repair.”
Diamond’s maintenance training course teaches all participants how to actually make a composite repair.
“With the training we give them, they’re capable of handling typical minor repairs,” he explained. “Major structural repairs do require specialist knowledge, as does major sheet metal repair. There are several competent and qualified shops throughout the U.S.”
Diamond works closely with repair facilities.
“The modular design, for example, is easily disassembled with left and right wings, stabilizer and interchangeable control surfaces; the recovery is simple and low cost,” he said. “In extreme cases of damage, components could be replaced, instead of repaired to minimize downtime and expense.”
Maurer said in order for any OEM to manufacture all-composite planes, they have to be set up to do that.
“You can’t just take a metal aircraft that was designed a long time ago and just change it into a composite aircraft,” he said. “You design the aircraft around the capabilities of the material. If you’re trying to build economically out of metal, you try to bend the sheet metal in one direction. With a composite structure, you can easily build compound shapes and you can optimize aerodynamics. In fact, if you look at the glide ratio between a DA40, compared to a Piper PA-28 or a Cessna 172, it’s far higher. What that means is that on the same fuel burn, you can get far better performance, or for equal performance, you can get less fuel burn.”
The D-Jet—not for Part 135 operations
The D-Jet, a five-place, single-engine fanjet Diamond is currently in the process of developing, isn’t designed for Part 135 operations, but for the “owner/pilot.”
“The D-Jet’s maximum ceiling is FL250 and cruise speed is 315 knots,” Maurer said. “It’s not designed to be the fastest nor the highest flying VLJ, but it’s designed to be safely operated by an owner/pilot with moderate experience and skill levels.”
The current deposit for the D-Jet is $20,000; however, he said that deposit “is against actual delivery positions.”
“We have quite a few down payments at this point, but at this stage, we haven’t even begun to advertise it,” he said. “We sort of put a little picture in with the other ads, but we don’t actively push it. The $20,000 deposits are ‘non-escrow’ deposits. The position holders know that the price might change, based on actual production cost, equipment, configuration and escalation. When we get closer to certification, the deposit will increase to ten percent and the price will be fixed. If someone were unhappy with the offering at that point, we’d certainly be very customer friendly.”
Diamond handled the DA42 in the same way.
“We’ve had very good response with customers displaying a high degree of confidence in Diamond,” he said. “Currently, Diamond is holding well over 100 deposits, without any D-Jet specific marketing effort. We would consider a D-Jet specific marketing program premature at this point. We’re not relying on deposits to sustain our development activities or attract external investors for the program.”
Diamond doesn’t believe in holding deposits in escrow accounts.
“It protects Diamond’s customers; it discourages investment speculators from trying to sell their early production slots for a higher price,” he said.
This is similar to people who buy hundreds of tickets to sporting events, then stand outside the event “scalping” them for much higher prices.
“Diamond wants to ensure that a delivery slot goes to the pilot who will fly that plane,” he said. “And reflecting our intended market, although the D-Jet isn’t designed around Part 135 air-taxi operations and regulations, it will, however, be equipped with very sophisticated avionics, weather, terrain and traffic information systems.”
When asked if the company can really build its light jet for under $1 million, Maurer commented that it’s a single-engine jet.
“If you look at the cost of an engine and the associated systems, as soon as you go to a twin-engine jet, you’re greatly increasing the cost,” he explained.
He said limiting the aircraft to FL250 means simpler systems, simpler emergency procedures and simpler structure.
“We would not design a single-engine jet with a super critical airfoil that was designed to fly at FL410 with high approach speeds,” he said.
People have questioned why Diamond isn’t building a twin-engine jet.
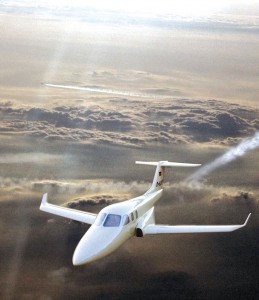
Diamond’s D-Jet, an all-composite, five-place single-engine VLJ, will meet its 2007 customer delivery forecast.
“If you look back at the turboprop market, there was never a single-engine turboprop, but then Cessna came out with the Caravan, Pilatus did the PC-12 and Socata came out with its TBM-700,” he said. “Today, there’s so many more on the market, no one bats an eye about a single-engine turboprop flying around. The D-Jet is aimed at that class of aircraft, and it’s not even at a level of a PC-12. The PC-12 is above the D-Jet by a long shot in terms of load-carrying capacity and size of the aircraft. However, if you look at someone who flies a TBM-700, a Malibu or any one of these small, high-performance turboprops, or current high performance singles or twins, those people would be a candidate to fly the D-Jet.”
He said if Diamond kept the system simple, under $1 million was a realistic figure.
“We’re confident we can do that; we certainly know what the cost is to build an airframe,” he said. “If you look at the DA42 Twin Star, priced at $439,000, it has a lot of structure to it for the price—an all-glass cockpit and four seats. But of course, adding a jet engine and producing the D-Jet will add some cost; the jet will be more sophisticated, but it’s a long way from $439,000 to $1 million.”
Maurer explained Diamond can easily build a jet for that price, without having to produce “high quantities” to meet that price because they can comfortably build about 100 aircraft a year.
“Building about 100 aircraft a year would be a viable project,” he explained. “We don’t have the level of investment in tooling that some other OEMs have in this segment, which requires them to build extremely high quantities to make it a viable project.”
Diamond has selected the Williams International FJ33-4 fanjet engine for the D-Jet, but a decision on whether the avionics would come from Garmin or from Honeywell hasn’t been made.
D-Jet’s progress
Initially, Diamond had forecast first flight by April 2005 and certification by year-end of 2006; however, that may not be the case.
“These dates have slipped nominally; however, our target of significant initial customer delivery rate for the D-Jet, commencing 2007, stands,” he explained.
Adam Aircraft Industries hopes to certify its A500 twin-engine, piston-powered pusher by year-end, and forecasts certification sometime in 2005 for the A700, a twin-engine jet powered by Williams’ FL33-4. When Eclipse Aviation began its 500-jet program, they forecast certification years sooner; switching to Pratt & Whitney versus Williams’ engines, though, put them behind the eight ball. Several OEMs have anticipated certification dates and most all of them have had delays for one reason or another.
“In our case, we’re not backing off the delivery date of 2007, and there’s a big difference between us and new companies not currently in production, such as Adam, Eclipse, Safire, Avocet, etc., in that we’re already producing certified all-composite airplanes,” Maurer says. “The D-Jet is an expansion of our product line; there’s no issue of whether we can do this or not. We have been doing it for a very long time. I do forecast FAA certification for 2007.
“The D-Jet is generally on target, although there have been detail milestone delays associated with a revision of the work share between the North American and European Diamond facilities. Delays on the DA42, certified in May 2004, in time for the Berlin air show, did affect the planned technical resources assigned to the D-Jet program.”
The detail milestone delays he refers to are “prototype construction, which involves first flight and selection of avionics and other suppliers.”
“The revised work share will bring more resources to the program, which will allow us to realize the end goal—significant number of customer deliveries in 2007,” he said.
Maurer said earlier reports indicating design changes made to the D-Jet’s fuselage, allegedly causing delays, are false.
“From the time of conception, you always go through a few alterations, but there were no significant design changes from the original concept,” he said. “The pressure vessel is forward of the engine, then you have a structure that runs back that carries the tail and the engine; the engine is under-slung that structure and it’s always been that way.”
Initially Diamond wanted to market the DA42 program earlier, but it ended up being certified 18 months after first flight, which in turn was 55 weeks from the beginning of the project.
“Still, that’s a very aggressive program,” he said. “If you look at some of the other manufactures that are doing VLJs, most have never produced an aircraft before. We’re not a startup; we have certified production facilities. We’ve gone through the type certification processes before. I’m not saying that the D-Jet won’t be the most complex project we’ve ever done; it certainly is, but progressively we’ve been working our way up. We’re growing and we certainly know how to certify aircraft.”
He confirmed that the first test vehicle prototype is being put together.
“Two months ago, when I was in Europe, I personally saw the full-size plugs for the D-Jet’s fuselage being put together,” he said. “First, we’re doing this off of a mock-up; then, we’ll get everything where it’s supposed to be and build the first flying prototype. The first flying prototype is not necessarily in a final production configuration; this is the case for all OEMs. First flight doesn’t incorporate all of the systems that the final aircraft would have. We have about 30 engineers and various support staff; it’s a lot of work, a lot of funding. Either you have many engineers taking a short time or you have a few engineers taking longer.”
Diamond, including its predecessor HOAC, has produced over 2,500 certified composite aircraft since 1981.
“We have all elements in place to design, certify and put into production a new aircraft model,” he said. “As opposed to a startup from scratch, we’re simply expanding our existing product line.”
He agreed that anyone could build a prototype and get that first plane off the ground, but for would-be OEMs, that’s when the wheels usually come off.
“They don’t have the funding or backing of an existing company that already certifies aircraft,” he said.
He also agreed that numerous startup companies assume people will take them seriously if they simply announce they’re going to produce an aircraft, or that there’s going to be a “first flight.”
“The airframer takes the lead in the project, but overall, it’s a collaborative effort with avionics, engine and other suppliers in addition to numerous engineer man hours,” he said.
The D-Jet in the U.S.
Maurer said Diamond customers have “heavy interest” in the D-Jet, and he believes it’s going to be highly successful in the U.S., because it’s “different, filling a market segment that’s been ignored,” and because it’s being produced by a solid company already making aircraft.
“Yes, I think we’re going to sell quite a few in the U.S.,” he said. “If you take a look at all the other ‘little’ potential VLJs out there—Safire, Avocet (both questionable), Cessna’s Mustang and even the Eclipse—they’re in a category that basically takes an existing business jet, which is really designed to fly at FL410, and they have ‘shrunk’ the aircraft down. If you look at our aircraft, the premise is different. It looks like everyone else’s; it’s a little jet, so everyone lumps us into the same category, but it shouldn’t be in that category.”
He said the D-Jet was never designed to fly at FL410.
“We didn’t take an original design and shrink it down,” he said. “We’ve always designed this aircraft to fly at a maximum of 25,000 feet. There are significant reasons for that, one of which is that at 4,700 pounds of maximum takeoff weight, it’s the lightest of any of the VLJs in that category. It’s absolutely an entry-level jet.”
He said that pressurization is not nearly as critical flying at FL250 versus FL410, which was another consideration for the aircraft’s design.
“At FL410 you can get very high speeds and fly over severe weather. At FL250, you might not always have the same advantages, but the way we’re looking at it is that this aircraft will be used more for short and medium ranges,” he explained.
Maurer doesn’t believe that a lot of the VLJs are going to get up to FL410 in the first place.
“Another thing is that many of these jets are operating at speeds that are significantly slower than commercial traffic—the airliners,” he said. “We see more conflict with air traffic control because of that. In designing the D-Jet, we’re not trying to fly the fastest or the highest; we’re appealing to a very broad number of people. This is a jet that is actually obtainable and will fly at a 315-knot cruise speed; that’s the target. It’s slower than the Eclipse 500 or the Mustang, but it’s still fast for a personal-owner-flown aircraft.”
There are also higher structural requirements if you fly above FL250.
“If you’re running at high attitude, you’re looking at about 12 PSI (pound per square inch) pressure differential or more, but if you’re flying at FL250, you’re looking at about 5.5 PSI, which makes the structure of aircraft lighter to build,” he said. “We can build a lighter structure using our composite technology. Another problem you could have flying above FL250 is that sometimes you run into stability issues. You sometimes need stability augmentation systems or boosted flight controls. We want to stay away from that with the D-Jet because the more complex the systems, the heavier the aircraft has to be; you’d need more power, more fuel.”
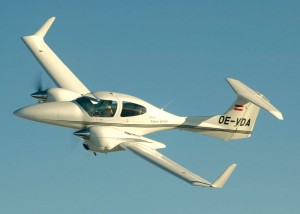
This DA42 Twin Star, certified in May 2004, in time for the Berlin Air Show, proves that the company’s composite xexpertise dating back to 1981 has paid off.
He added that Diamond had weighed the benefits of making the D-Jet more complex, but determined that if they made it heavier and more complex, the cost would significantly be higher.
“That would narrow the use of the aircraft for a small percent of missions or for a small percentage of people,” he said. “That’s why we’re not initially looking at the air-taxi market; we want the owner/flown, private owner segment. That’s the missing link.”
Maurer explained that another reason to cap flying attitude at FL250 was the design of the D-Jet’s wing.
“If you look at a picture of the D-Jet, the wings may look as if it’s a swept design, but they aren’t; it’s a straight, tapered wing,” he said. “The airfoil is designed for a good glide and low stall speed of 64 knots, so you have low approach speeds.”
He said because of aerodynamics, the aircraft would be stable, easy to fly and have excellent handling characteristics.
Diamond’s safety philosophy and chutes
Maurer said a report of the current concept to include an airframe parachute system for the D-Jet is false.
“It’s not possible to use current technology airframe parachute systems because of the speeds involved with the aircraft, but if a higher speed capable system were to be developed, we’d certainly consider its integration,” he said. “I think it’s fair to say that if there were such a system available, naturally we’d look at it—no question about that. We have talked to BRS about this; they are working on other developments for the future. I can’t speak for them, but if there’s suitable technology, it’s certainly something that would be considered, but that’s as far as I can go.”
Diamond has a three element safety philosophy in which they approach safety issues.
“There’s active safety, passive safety and what we call continuous review of safety-related field experience and retrofit modifications, if necessary, to look at after a situation has happened,” he said. “Active safety is all the elements that help prevent an accident in the first place. Passive safety are the elements that help prevent injury in case an accident has already happened. A ballistic parachute recovery system is a passive safety device. When you pull the chute, something has already happened—sort of like an airbag going off in a car. It’s a passive safety device because something has already happened to cause the car’s airbag to go off.”
Diamond doesn’t offer a parachute system on the piston-powered DA40 because they focus on active safety.
“That means accident avoidance, in the first place,” he said. “In fact, if you look at our accident history on the DA20 and the DA40, we’ve got an accident/safety history that I think is not matched by anyone else in the industry. We have an excellent relationship with the product liability underwriters as well, and knock on wood, we’ve never had a claim to date against our product liability policy.”
He said that since 1993, when the DA20 became available, they’ve had two fatal accidents.
“To date, we have had no fatalities and no injuries in the DA40,” he said. “Our aircraft have high utilization; we have over 1.5 million fleet hours on the DA20 and we’ve manufactured about 600 of those aircraft and manufactured just over 450 DA40s.”
As far as flight and ground school training and safety, Diamond works with nearby flight schools in Canada, and provides factory training as well.
“We plan to expand our DA42 training, and before the D-Jet is made available to any pilot, a comprehensive training syllabus will be established,” he said. “I expect we will have full simulator training before anyone gets into the jet, and as well, ground fight training programs will be implemented. The type of simulator will depend greatly on the requirement of the training providers; we’ll have professional and reputable flight training providers conduct the training rather than do it in-house.”
Maurer cautioned that getting too caught up in whether the sim is full-motion shouldn’t be the only basis of excellent flight training.
“There are fixed-base simulators that are better than some low-cost, motion-base simulators,” he says. “The best simulators are, of course, the highest fidelity motion-base simulators, but the airliner ones are typically in the 10- to 15 million-dollar range. They use these because it’s prohibitively expensive to be flying around an airliner for training.
“With something like a D-Jet, a combination of fixed-base training and actual flying could be easily as good as or better than training in a low-cost motion-base sim. The key to the training success will be the quality of the syllabus, the quality of the instructors and periodic recurrent training for the owner/pilot. It’s very important to stress the importance of teaching risk management and having pilots recognize and respect limitations that are consistent with their skills and experience.”
Additionally, he said as far as safety and what insurers should be looking at, it is “what are people stepping out of.”
“You can’t compare commercial airliners to owner-flown aircraft in terms of accidents, incidents or safety,” he said. “Essentially, we believe that our customers will step up from single-engine turboprops, potentially, multiengine turboprops, multiengine pistons and high-performance singles.”
Maurer is a firm believer that when pilots move up from those types of aircraft, providing low-stall speed, good low speeds and stable handling characteristics, combined with simple systems, sophisticated avionics with traffic collision avoidance, weather systems and a turbine engine, the aircraft will be much safer.
“We all know that the FAA requires a type rating to fly a turbine aircraft, but below that classification, you really don’t need a type rating,” he said. “Again, training is very important.”
He said you could go out with your PPL and fly a high-performance single, and if you stick a low-hour pilot into a Lancair C-400, a Cirrus SR22 or a Bonanza, “they’re going to be in over their head.”
“Anyone can purchase a 500-horsepowered Ferrari, but that doesn’t mean you’re qualified to drive that car,” he said. “A lot of them have ended up in the ditch!”
- Diamond’s two-seat, no nonsense DA20 trainer is used by numerous flight schools. Embry-Riddle Aeronautical University plans to teach 500 Air Force cadets annually how to fly at the Air Force Academy in Colorado Springs.
- Diamond’s DA40, a four-seat, single-engine all-composite aircraft, has the option of upgrading to an all-glass cockpit.
For more information, visit [http://www.diamondair.com].