By Shari Valenta
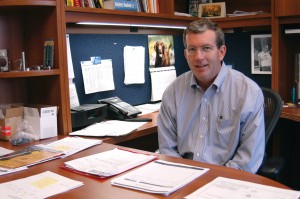
Grady Cope started Reata Engineering and Machine Works by charging $6,000 to his credit card 12 years ago. Now he has nine machines and 27 employees in his 25,000-square-foot facility.
Reata Is Reliable
Need machined parts for your business? Reata Engineering and Machine Works is committed to completing projects on time. Reata is a contract manufacturer specializing in precision machining and assembly. They do the turning, milling, grinding and assembling involved in manufacturing anything from parts used in medical instruments to airplanes.
There are three engineers on staff that specialize in CNC production (using computerized production carving equipment). Engineers work with customers to design prototypes and suggest ways to cut cost of production parts. There are eight CNC production machines and one CNC coordinate measuring machine on site. Twenty-seven employees operate two shifts in this 25,000-square-foot facility. Grady Cope, owner and mechanical engineer, started the business from the ground up, upon advice from a friend.
“After graduating college at the University of Colorado at Denver for engineering, I went to work for the Gates Rubber Company,” he said. “I worked there for six years but never fit into its big corporate culture. One of our vendors said he wanted to retire working as a machinist. He recommended I think about doing it myself and he’d sell me his customer list.”
Before college, Cope was a mechanic and worked off shore for Halliburton, one of the world’s largest providers of products and services to the oil and gas industries, so he had mechanical experience.
“I bought a manual mill and a lathe on my credit card for $6,000 and started machining at night,” he said. “A couple of months later, I resigned from Gates, and then Reata became a reality.”
Cope enjoys owning a business because he can work with his family. His wife, Anne, and his two Labrador Retrievers occupy an office down the hall. Mrs. Cope owns Corey Electrical Engineering, Inc. The couple has paired up on some projects such as crafting end caps for some of Corey’s lighting fixtures.
Cope’s business makes parts big and small. Production runs can be from one to 40,000 and average about 500 pieces.
“The smallest item we made barely fits on my fingertip, and it was made with the biggest machine here,” remarks Cope shaking his head. “However, most of the stuff we manufactured can be held in one or two hands. The biggest item is a hoop that is used to make the chips for computers.”
Cope says his company separates itself from other machine shops because they guarantee projects to be completed on time.
“If we’re late on a delivery, we penalize ourselves,” explained Cope. “For example, if we’re late by a day, the customer will pay only one half of the quote. We self penalize for as much as $500 on a four-week delivery if we’re late. By doing this, we’re telling our customers that they’ll get the parts when they need them. If they need them in a week, we’ll guarantee that we’re going to do that, if it’s possible.”
What’s on time? Regular turnaround time is three to four weeks, depending on the project. However, customers can opt to pay more for a one-week turn around.
“One time a customer called on a Thursday night, and ordered three parts we’ve never made before,” recalled Cope. “The material wasn’t available in Colorado and they needed it done in a week, so we ordered the material from California that night and had the material air freighted. We machined the parts on Friday and Saturday, and we took Sunday off. We worked Monday morning, and then shipped the parts to Colorado Springs for plating. They came back on Wednesday.
“We shipped them to Fort Collins to be packaged in a clean room. We were able to pick them up on Friday morning and delivered them to our customer early that afternoon. The customer emailed me with a one-word response: ‘Awesome!’ That’s what we do on a regular basis; a lot of people want parts in one or two weeks.”
Cope says he continues to do business because he feels satisfied seeing his finished machined pieces everywhere.
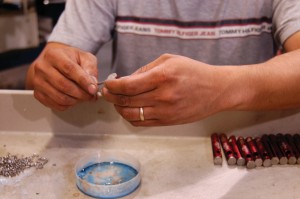
An employee at Reata performs the delicate work of making clips used in fly-fishing for Fishpond, Inc., Silverthorne, Colo.
“I’ve always had a passion for production because you create something out of nothing,” he said. “I went to visit a customer in Durango earlier this week. When I was down there I had a moment, so I decided I would visit some of the fly-fishing shops to see if some of the products we manufacture were there. It’s always so wonderful to go in and see a product that was made in your shop. It’s a pretty good feeling to know that you’re contributing. I love it.”
Reata has busily machined products for 12 years. It was formerly located in old town Englewood, but to facilitate expansion, relocated a year ago two miles east of Centennial Airport. If you’re looking for a reliable machine shop to contribute to your production, give Reata a call.
Reata Engineering and Machine Works is located at 7822 South Wheeling Court, Suite A. For more information, call 303-936-1350 or visit [http://www.reataeng.com].