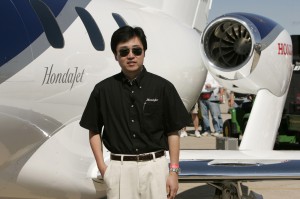
Michimasa Fujino, the HondaJet project leader and vice president of Honda R&D Americas, Inc., became Honda Aircraft Company’s president and CEO in October 2006.
By Henry M. Holden
For the past few years, several Japanese auto manufacturers have been looking at the general aviation market. Toyota certified an aircraft variant of its Lexus automotive engine in the 1990s, but never put it into production. Honda started its research more than 20 years ago.
Michimasa Fujino, considered the father of the HondaJet, began work on Honda’s aircraft program in 1986. His research project on small aircraft and jet engines was, in his words, a “pure home-grown effort.”
Fujino joined Honda in 1984, after graduating from Tokyo University with a degree in aeronautical engineering. He spent the first two years of his career in the automobile research division, working on the development of a new electrical control steering system.
When Fujino went into the aviation project, top management gave him the latitude to proceed with his ideas, something most aircraft manufacturers wouldn’t have done. However, Honda’s top management wasn’t happy when he first proposed his design.
Fujino proposed an unusual over-the-wing engine configuration, similar to one developed in the 1970s by Dutch aircraft manufacturer Fokker. The Fokker VFW-614, a 40-passenger Sabreliner-sized design, lacked enough orders to make it successful and was never put into production.
The over-the-wing podded engine configuration allowed for more space within the fuselage and a reduction in drag at higher speeds. Fujino suggested a fuselage made from lightweight composite materials—not a widely accepted engineering design at the time, especially for business jets. He struggled through many setbacks on the long road to the HondaJet.
Honda moves to the U.S.
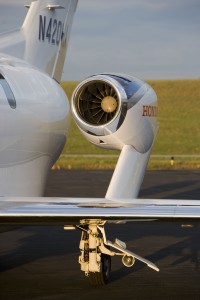
HondaJet’s patented over-the-wing engine mount reduces drag at high speed and improves fuel efficiency.
In 1993, Fujino and a small team of engineers relocated to the United States and began joint research with Mississippi State University on a twin-engine, six-seat, composite fuselage aircraft. Fujino led all engineering tasks, from design through experimental verification, fabrication and flight-testing of the HondaJet.
While some old-school experts felt small business jet engines and airframes had reached the limit of subsonic performance, Fujino stretched conventional wisdom to see if he could find a way to squeeze more speed and economy from an airframe. His proposal would eventually lead to a revolutionary design and disprove old ways of thinking.
This research led to the development of Honda’s MH-02, an organic matrix composite prototype. Honda and MSU’s Raspet Flight Research Laboratory fabricated and assembled the engine.
Fujino describes aircraft design as “much more challenging than auto design, given the critical nature of weight and the environmental issues facing aircraft operators.” The research continued until 1996, when Honda began high-altitude testing of its first generation turbofan engine, the HFX-01, conducting more than 170 hours of tests. Today, that engine is on display in a museum in Japan.

HondaJet will offer two interior configurations: the standard configuration with seating for seven (two pilots and five passengers) and the air-taxi version with seating for eight (two pilots and six forward-facing passengers).
Honda developed its own small turbofan jet engine in 1999. The HF118, developed in partnership with General Electric Aviation, was test-flown on a Cessna Citation. The engine featured a single fan, a two-stage compressor and a two-stage turbine. Additional design testing on wing shape and design took place on the modified wing of a T-33 Shooting Star. By bonding a polyurethane foam glove over the original metal wing, engineers were able to bond a fiberglass skin over the foam. Sensors and infrared cameras filmed the laminar-to-turbulent boundaries.
New design emerges
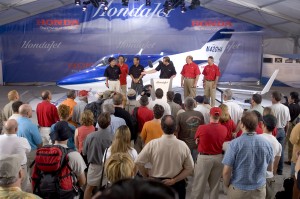
Michimasa Fujino conducted a HondaJet news conference at EAA AirVenture 2006 in Oshkosh, Wis. An enthusiastic crowd later watched the demonstration flight.
Fujino’s design was a literal nose-to-tail reinvention of the airframe. It included a natural laminar-flow wing section, a laminar-flow nose section, which reduced drag on the fuselage, and an over-the-wing engine mount. After years of computer modeling and wind tunnel testing, Fujino found that an engine pylon placed over the wing decreased drag, relative to a standard rear-fuselage engine mount design.
The construction of the passenger cabin was similar to a conventional aluminum fuselage, but the components were made of composite materials. To maintain the compound curves, the cockpit and tail sections were of honeycomb-sandwich construction, important for the laminar-flow nose section. Curing these materials separately, and then mating them, had been the normal process. But the patented co-curing process of the sandwich and stiffened panels in the autoclave reduced weight, drag and cost.
Fujino estimated the fuselage weighed about 10 to 15 percent less than an aluminum fuselage of similar size. He also proposed an aluminum main wing, derived from T-33 trials that used an integrally stiffened skin, resulting in a smooth wing surface that preserved the laminar flow.
Fujino spent about three years working to dispel conventional wisdom that said putting anything on the trailing edge of the wing would induce unacceptable drag and add unacceptable weight to the structure that must support an engine, its vibration and thrust loads.
Honda used its proprietary computational fluid dynamics software to optimize airflow within the compact engine, maximizing performance. The engine’s simple, high-performance combustion chamber kept emission levels low enough to meet the requirements of anticipated standards for compact jets.
Based on electronic control technology originally developed for automotive applications, Honda created the first ultra-compact Full Authority Digital Electronic Control system for this class of engine. It provided superior engine operation and reliability without variable mechanisms.
Finding the right spot and shape for the pylons was just the beginning of challenges facing Fujino. Flutter characteristics were also important. If flutter from engine vibration and thrust loads wasn’t compatible throughout the flight envelope and wasn’t properly managed, it could set up parasitic flutter that would interact with the flutter associated with the wing’s normal bending.
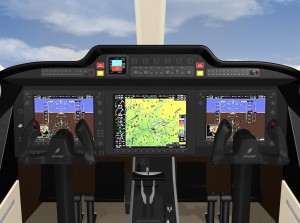
The HondaJet has an advanced, customized, all-glass cockpit, based on a state-of-the-art Garmin avionics platform. Like many of the other systems, the flight control system is conventional, with standard yokes.
The natural laminar flow airfoils reduced drag by keeping the airflow attached to the wing surface longer than with other airfoils. The National Advisory Committee on Aeronautics (the predecessor to the National Aeronautics and Space Administration) developed a series of natural laminar flow airfoils in the early 1940s. These early designs were mainly sensitive to leading-edge contamination from small particles such as bugs and ice. Even minimal contamination could dramatically increase drag, lowering speed and increasing fuel burn. In addition, the most efficient natural laminar flow designs used a thin wing, which didn’t hold as much fuel as the thick wings normally utilized at that time.
“The over-the-wing engine mount configuration liberates valuable fuselage space for increased room in the cabin and cargo stowage, while significantly reducing aerodynamic drag at high speeds, for major improvements in performance and fuel efficiency,” said Fujino.
Because the engines were adjacent to the rear cabin, Fujino wondered if the European Aviation Safety Agency and the Federal Aviation Administration would be satisfied with this arrangement. He worried if, in the case of thrown compressor blades, the agencies would demand rotorburst requirements, such as engine nacelle containment belts.
In October 2000, Honda R&D Americas, Inc. established a research facility at Piedmont Triad International Airport (PTI), in Greensboro, N.C. Its purpose was to research, fabricate and flight-test the HondaJet.
A veil of secrecy
For the next three years, Honda would play a strategic game of hide-and-seek. The nondescript white buildings housed a small group of engineers, flight-test personnel and company executives, who worked on the design, development and testing of the very light jet.
Except for some papers Honda published in 2002, detailing the technical achievements of the airframe, little else was known about what was being done at HondaJet in North Carolina.
“This small building is filled with very sophisticated technological abilities and big dreams,” said Fujino.
In 2003, Honda Motor Co. slightly lifted the veil of secrecy when it announced the development of its compact, lightweight, fuel-efficient, low-emissions HF118 turbofan engine for Honda’s experimental business jet. The HondaJet first flew on Dec. 3, 2003, just two weeks before the centennial of flight.
In 2005, Honda flew its prototype to EAA AirVenture Oshkosh for its world debut. It returned a year later, and Fujino conducted a technical briefing to share the most recent status of the HondaJet program.
Honda’s PTI facility went virtually unnoticed until October 2006. At the National Business Aviation Association’s annual convention in Orlando, Fla., Honda Aircraft Company announced that more than 100 individual customers had put down deposits for the $3.65 million HondaJet. This count included only individual orders, but many observers believe that significant interest exists from fleet operators, a group that includes fractional and air-taxi operators.
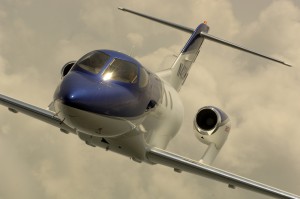
HondaJet, Honda’s innovative light jet, will hold six to seven passengers. Its innovations give it better fuel efficiency, a larger cabin, more luggage space and higher cruise speed than conventional aircraft in its class.
“Due to this overwhelming response, we’re now considering an increase in our production plan, to meet the needs of our customers,” said Fujino.
HondaJet will be offered in two interior configurations: the standard configuration with seating for seven (two pilots and five passengers) and the air taxi configuration with seating for eight (two pilots and six forward-facing passengers).
HondaJet’s cabin offers its passengers unprecedented levels of comfort, with as much as six inches more legroom per passenger than competitive offerings. The jet’s 57 cubic-foot aft cargo hold is up to 50 percent larger than the holds of other jets in its class. A 9-cubic-foot nose cargo hold provides additional cargo storage.
Key specifications and early performance figures establish HondaJet as the fastest and most fuel-efficient aircraft in its class. HondaJet features a class-topping cruise speed of 420 knots, with an IFR range of 1,180 nautical miles, and a 30 to 35 percent gain in fuel efficiency at cruise speed, versus other jets of comparable performance. HondaJet’s cabin is about one foot longer than even larger light jets, and it features a fully private lavatory, along with a spacious 57-cubic-foot aft cargo hold.
To date, HondaJet has logged more than 260 hours of in-flight testing with superior results. In December, Popular Science chose HondaJet as the winner of the publication’s 2006 “Best of What’s New” award in the aviation and space category. The HondaJet was chosen from among dozens of aviation products for its breakthrough design and innovative features, representing a significant step forward in its category.
Honda Aircraft Company is currently pursuing FAA type certification and production certification for its advanced light jet, with the goal of completing certification in three to four years, followed by U.S. production and the delivery of the first plane in 2010. HondaJet is projecting a production volume of 70 jets per year. PTI is a candidate for its manufacturing center.
The search for an assembly site
According to Ted Johnson, PTI’s executive director, Honda has inspected several 70- to 100-acre sites at PTI for a possible assembly site. Guilford County commissioners said in late January that the Honda Aircraft Company is seeking a total of $1.2 million in economic incentives from Guilford County and Greensboro, in addition to $100,000 from High Point, N.C., and $100,000 from a group in Winston-Salem, N.C. The Honda plant would employ about 300 people at an average annual salary of $72,000.
“Honda has identified the Greensboro area as one of several locations in the United States being evaluated as a potential site for expanded operations,” said Jeffrey Smith, the assistant vice president for corporate affairs for Honda in the United States.
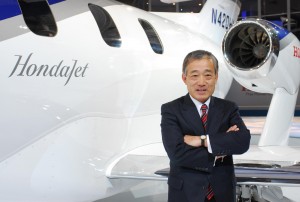
Takeo Fukui, Honda Motor Company president and CEO, announced the sale of HondaJet at the NBAA convention in Orlando, Fla. Honda set the price for the advanced light jet at $3.65 million, and plans delivery in 2010.
The HondaJet will be sold through five regional sales groups—HondaJet East, HondaJet Southeast, HondaJet Midwest, HondaJet Southwest and HondaJet Northwest. Fourteen offices will be operated around the country. HondaJet developed a dealer network in collaboration with Piper Aircraft, Inc., in its business alliance announced in July 2006.
Honda Aircraft Company will also seek to establish a network of service facilities within a 90-minute flight time from any location in the U.S., to further advance its goal of creating a new level of customer service and support. Honda and Piper both assert that their respective jets will not compete, because markets and pricing structures are different.
At the 2006 conference, Fujino shared his memories of an NBAA conference 20 years earlier.
“I attended NBAA for the first time in 1986,” he said. “If my memory is correct, it was held in Anaheim, Calif. I was a young aerospace engineer, just out of college. Japan has no event such as NBAA. So, I vividly remember that when I entered into the exhibition center, the gorgeous exhibits and the stunning business jets struck me. From that time on, it has been my dream to bring a jet I designed to this magnificent show. Twenty years later, I’m very proud to present to you the results of Honda’s dream to enter the aviation industry.”
Fujino has fulfilled his dream and has another goal.
“Just as we have targeted real innovation with HondaJet design itself, we’re equally committed to creating an innovative sales and service network,” said Fujino. “Now, I’ll do my best to deliver an aircraft of outstanding performance and quality to all our customers.”
For more information, visit [http://www.hondajet.com].