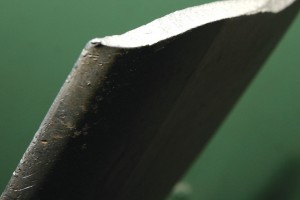
This propeller lost four inches from the tip when a stress fracture grew from a nick in the leading edge.
By Reggie Paulk
On April 19, 1993, a plane crash claimed the lives of eight people, including the governor of South Dakota. The findings from that crash would shed light on a problem that still threatens flying safety.
At 24,000 feet, the Mitsubishi MU-2 was cruising in level flight when a violent explosion rocked the airplane. In an instant, a gaping hole was torn in the side of the fuselage, and the cabin depressurized. An undiscovered fatigue crack in the propeller hub had propagated to the point where the hub failed, releasing a propeller blade. The resultant imbalance in the propeller disc caused the engine to be partially torn from its mounts, inflicting massive damage to the nacelle and wing. The free propeller blade tore into the fuselage, immediately causing grave injury to one of the passengers. The damage caused by the failure resulted in such dramatic aerodynamic losses that the flight crew was unable to maintain altitude with the good engine, eventually resulting in a collision with a silo, destruction of the aircraft and loss of all on board.
Two years later, a similar set of circumstances claimed the lives of eight more people onboard an Embraer commuter aircraft. In this instance, a fatigue crack in one of the left propeller blades resulted in loss of the blade and destruction of the left engine nacelle and wing structure. Again, the aircraft was unable to maintain altitude due to the damage, and crashed short of an airport. Because of the loss of life, and the high profile of one of the victims, these accidents spotlighted a dangerous and overlooked problem in the airplane industry: propeller fatigue.
For most pilots, the propeller isn’t much more than an item on a checklist during a pre-flight inspection. It’s also a handy place to grab onto while trying to push or pull the airplane into a tie-down spot. Beyond making sure the propeller has no major dings, we rarely give it much thought. After engine start, it becomes a blur, and the old saying, “Out of sight, out of mind,” applies.
Russ Kessinger of Aero Propeller & Accessories, Inc., based at Rocky Mountain Metropolitan Airport (BJC), knows a lot about good propeller maintenance. In more than 30 years working with propellers, Kessinger has witnessed every possible issue that can crop up.
“A metal propeller acts similarly to a tuning fork,” says Kessinger. “It transmits the harmonics and frequencies from the engine down the propeller blade.”
In fact, these harmonics may cause the propeller tips to flex three to four inches fore and aft.
“It’s similar to holding a fishing pole horizontally and shaking it up and down,” continued Kessinger.
In addition to fore and aft movement, up to 20 tons of centrifugal force act upon the propeller hub and blade retention components during flight. That’s like hanging a full dump truck off one blade. Add to that uneven power pulses of pistons firing, along with aerodynamic loads, and you have components under immense strain the entire time they’re in use. Propellers are engineered to endure these stresses, but improper maintenance, neglect and the passage of time add up, and may eventually lead to failures.
Walter infiltration
Coloradoans assume the dry air helps preserve metal. Moisture is a necessary component of rust and corrosion processes, so the less present the better. Kessinger dispelled any myths about Colorado’s superior air by displaying a variety of propeller components in different stages of decay.
Variable pitch and constant speed propellers ride on hardened steel ball bearings. These bearings allow the blade’s pitch to change in flight. One such set displayed by Kessinger had rusted so badly that the propeller couldn’t even change pitch. This particular airplane had lived its entire life in the dry air of the Rocky Mountains, and the propeller was only 6 years old. How is that possible?
Water infiltration occurs from four sources: pressure washers, rain, condensation and grease. Pressure washers used near a propeller hub exert enough force to blast water past gaskets, seals and grease, damaging sensitive metal components within the hub. Kessinger’s advice: never use a pressure washer on an airplane.
A propeller stored with its blades in a vertical position will channel rain into the hub. The standing water eventually makes its way past gaskets and seals. Condensation will occur any time the temperature of the propeller assembly drops below the dew point. Finally, grease acts much like a sponge, according to Kessinger. Over time, grease absorbs moisture and breaks down, making its regular replacement a good preventive maintenance procedure.
Aluminum components
And what of the hub’s aluminum components? Corrosion and stress fractures are common occurrences. One such hub had a stress fracture that went from inside, through the hub, out to the mounting flange. Had it propagated any further, it would’ve led to a catastrophic failure of the entire assembly, very similar to the MU-2 incident mentioned earlier. That same hub assembly had a blade-retaining ring with corroded threads. Kessinger noted the ring, once mounted in the propeller assembly, has a torque specification in the hundreds of foot-pounds. Corrosion concentrates stresses and may lead to a catastrophic failure of the component.
The tuning fork effect of the propeller concentrates stress in blade anomalies. One blade from a constant speed propeller was missing four inches of metal from the tip. What had started out as a nick (not a gouge) on the leading edge progressed into a crack, ultimately leading to separation. The leading edge of the blade had many nicks into which a dull pencil could fit; the paint along the edge was worn away and the bottom blade surface had many small nicks from gravel strikes. What was most interesting about the blade was that it didn’t look much different from blades on many airplanes out on ramps today. The tuning fork effect will also concentrate stress in areas of corrosion anywhere on the blade surface, with the same possibility of stress fractures developing.
Because propellers are mounted to a crankshaft or gearbox, they’re actually part of a much larger system that includes the engine and engine mounts. Aerodynamic loads and engine pulses induce vibrations into a propeller that are accounted for during the design of the propeller—but only on a relatively fresh engine, with engine dampers in good condition. Worn or damaged engine dampers produce additional harmonics, which contribute to metal fatigue in the propeller, not just the crankshaft and other engine components.
Did you know a tachometer could cause a propeller to fail? Kessinger pointed out that many tachometers might indicate as much as 100 to 200 rpm from the actual engine rpm. That means you could be over-revving your propeller, or operating within a restricted rpm range, without being aware of it. Any problems already present can be exacerbated. Depending on the amount of discrepancy, a propeller may need a full teardown and inspection. Have your mechanic check the accuracy of your tachometer at every annual.
Variable pitch and constant speed propellers present their own set of challenges. Additional moving parts offer more opportunities for failure. Additionally, the mechanisms used to change propeller pitch are tied to the engine’s oil system, so additional precautions must be taken.
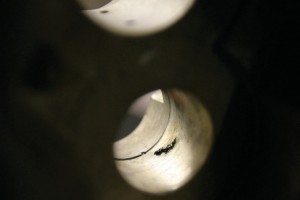
The gouge inside this propeller governor is advanced corrosion; it would’ve gone undetected during even the most thorough annual inspection. A hole in the governor can lead to engine seizure due to oil loss.
Constant speed and feathering propellers use a governor to regulate the amount of engine oil sent to a piston in the prop hub. With feathering propellers, oil pressure pushes the piston, reducing the pitch of the blades, causing the engine to turn at a higher rpm. Lower pressure causes the blades to increase pitch, decreasing rpm.
With constant speed propellers, the operation is the opposite. The propeller governor plays an important role in maintaining proper oil pressure; if its internal pressure regulator fails, control of the propeller can be lost, or in the extreme, the cylinder assembly of the propeller may rupture. That is essentially like opening the oil drain plug and pumping engine oil overboard at 290 psi, (the rated output pressure of most governors). A rupture of the propeller cylinder results in an almost immediate need to shut down the engine, not to mention a couple gallons of oil covering the windscreen.
Corrosion
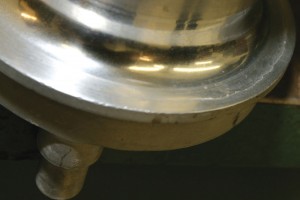
The uneven line running along the right side of the propeller shank is a crack, a common occurrence among older propellers. The only way to find it is to disassemble the propeller hub.
Corrosion can also be an enemy of the governor. Kessinger had a governor on hand with internal corrosion so advanced it had almost penetrated through the assembly, creating another potential oil drain.
If you have a fixed-pitch propeller, don’t think it’s immune from corrosion or fatigue. When was the last time your mechanic removed the safety wires from the propeller bolts, removed the nuts and looked at the backside of the propeller? Have the bolts recently been re-torqued to the proper specifications? Was the spinner assembly checked for proper torque and cracks?
This may seem like doom and gloom, but education is the first step toward prevention. If you own an airplane, or know someone who does, it’s time to scrutinize the propeller. Annual inspections carry no mandate for the removal and inspection of the propeller, unless there’s an airworthiness directive affecting that propeller.
One reason propellers are often overlooked during an annual inspection is because FAR Part 43 doesn’t clearly state what should be done. In accordance with the Code of Federal Regulations, Title 14, Part 43, the following items are to be checked at the annual inspection: propeller assembly for cracks, nicks, binds and oil leakage; bolts for improper torque and lack of safety wiring; anti-icing devices for improper operation and obvious defects; and control mechanisms for improper operation, insecure mounting and restricted travel.
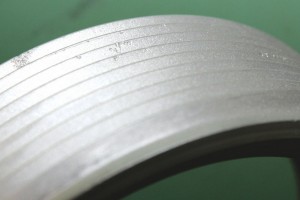
Corrosion caused the small pits along the threads of this propeller-retaining ring. This highly stressed part is subject to failure when corrosion develops.
Kessinger notes the attention the propeller receives during an annual inspection puts the aviation mechanic in a precarious position. Outdated procedures do not address corrosion and the associated problems corrosion causes. Historically, guidance for mechanics in the field has been inadequate. As a charter member of the Worldwide Aircraft Propeller Association, Aero Propeller was instrumental in producing FAA Advisory Circular 20-37E. This free document contains more than 30 pages of information about propeller maintenance, including detailed drawings and color photographs. If nothing else, the photographs in the document make quite an impression. Rust, corrosion, pitting and other ailments are covered in detail, as well as their prevention and mitigation. Ask your mechanic to review the AC before your next annual inspection. Since education is the first step toward aviation safety, Aero Propeller conducts training classes for Westwood College students and mechanics in the field.
Prop Saver Program
Realizing the safety and economic impacts a detailed inspection of the propeller can have on an aircraft owner, Aero Propeller has developed their Prop Saver Program for the Part 91 operator. With this program, the propeller is disassembled, cleaned and visually inspected for abnormal wear, corrosion or unairworthy conditions. The blades are stripped of old paint and new corrosion protection and paint are applied. The propeller is reassembled with new seals and lubricants and then balanced. Although not considered an overhaul, which should be accomplished on a periodic basis, the program can add years of reliability and safety to the propeller by minimizing environmental and operational effects.
The cost of this program is approximately half the cost of an overhaul, enabling the owner to have this propeller inspection accomplished on a regular basis. Aero Propeller has been maintaining and servicing propellers for more than 30 years. I there’s a component or operational problem, they’ve seen it and will be able to give you expert advice on a repair.
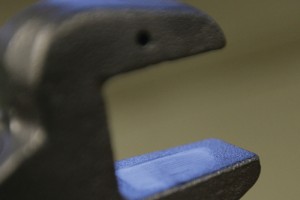
This fork changes the pitch of the blades in flight. The scoring along the bottom fork introduces harmonics into the propeller system due to out-of-tolerance operation.
Don’t think that metal propellers are the only ones affected by neglect. Both wood and composite propellers are subject to their own problems. Composite propellers still have metal hub components that are subject to corrosion and rust. Wood propellers are highly susceptible to moisture penetration. The good news is that, no matter the material, Aero Propeller will maintain and repair it. With a fully equipped composites shop, they can repair a small pit in a composite propeller blade or repair a composite structure.
A recent visit to YouTube.com revealed a video of a propeller failure. In the video, the airplane is flying along normally. Suddenly, a huge explosion rocks the airplane as one blade departs, and it begins to shed parts. The pilot immediately reduces rpm and shuts the engine down. As the propeller is spinning down, the vibration practically rips the instrument panel from its mounts. Happily, the airplane was on a test flight over an airport, and the pilot was able to land safely. Had the incident occurred right after takeoff over a populated area, or if the engine had been torn loose, the results could’ve been disastrous.
Propeller maintenance is a responsibility of the owner. Don’t let a lack of mandates for propeller inspection and overhaul lull you into a false sense of security. Have the propeller checked, and make sure it’s on a regular schedule of inspection.
To learn more, visit [http://www.aeropropeller.com] or call 303-469-1749.