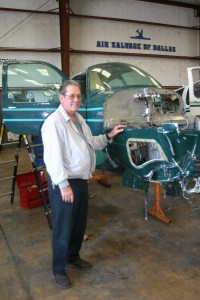
The 35 Bonanza behind Paul Camp, Air Salvage of Dallas president, is donating its useable components and avionics.
By Daryl Murphy
As aircraft parts and avionics become increasingly expensive and often harder to find, many owners and repair facilities are turning to parts salvaged from wrecked aircraft. The prospect of using components off an airplane that has had major airframe damage, however, dissuades many pilots from even considering a “junkyard” source, but rest assured, it’s all aboveboard, safe and sound and, of some importance, economical.
“Today, fewer factories are furnishing parts support for older aircraft,” explained Paul Camp, president of Air Salvage of Dallas. “When we get an aircraft, we remove all serviceable parts and inspect and clean them and put them in stock. We don’t knowingly ship non-airworthy parts.”
Located adjacent to Lancaster Airport (LNC) south of Dallas since 1974, Air Salvage has a rotating stock of several hundred recovered aircraft on its eight-acre site, primarily piston singles and twins, but with a growing number of turbines.
“When we send out a good part, we also send a used part tag with it that lists the model from which it came and time in service,” Camp said. “We also keep a record of every part. The tag is required for Part 135 operations, but not for Part 23. If it’s an airworthy part, after it’s installed, an A&P must sign off on it.”
In general, the FARs allow an owner to install most parts, usually under the supervision of a certified mechanic. When a salvaged aircraft is delivered to ASOD, its wings are stored in an open-front building, sorted and shelved according to make and model. The fuselage is then put into the shop, where the engine and most other major parts and assemblies are removed. After it’s down to the essential airframe, the fuselage is parked outside in neat and tidy rows—again by make and model.
Engines
Besides being the heart of an airplane, engines are at the center of business at ASOD. After they’re removed from the airframe, power plants are inspected and cleaned, put on a test cell and run from two to five hours to determine condition and to find any hidden defects. Results are documented and will be furnished to the buyer. Pricing is pro-rated on total engine hours.
“If an engine has a defect, it’ll talk to you on the test stand,” Camp said. “We’ve been fortunate over the years. Only two customers have had problems with an engine they got from us. In both cases, it was because the installer had changed the parts that caused the problem.”
Most of the popular Continental and Lycoming models are in stock, and once in awhile, a radial salvaged from a Model 18 or ag-plane. But Camp has one engine that he’s not sure how to sell.
“It’s a Hirth, out of a homebuilt,” he said. “It seems this homebuilt was heavily damaged in a shop accident, and we ended up with it. I don’t know anything about the airplane or the engine, but I know that a certified airplane is built to a standard, while a homebuilt is built within the talent and limitations of the builder, so it can be an unknown. But, it is for sale!”
Business founded out of frustration
Camp and Lucky Louque, his general manager, started the business 33 years ago as a result of trying to find parts for a Cessna 170 they were rebuilding. Constrained by a lack of parts sources, they bought a 170 that had crashed in Central Texas, rented a trailer and went to retrieve it.
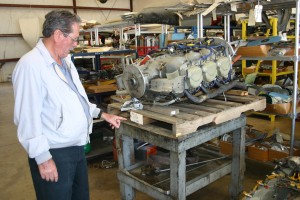
Paul Camp points out a low-time engine that will be run on a test stand for two to five hours before being released for sale.
The problem was that no one could give them advice on recovery techniques. By the time they had figured out the logistics of lifting and loading the airplane onto a trailer and dragging it several hundred miles on an interstate highway, they both had learned a great deal. As their business expanded, they discovered more and more specialized retrieval techniques.
Within a few years, Air Salvage of Dallas had developed a reputation for quick, organized and thorough aircraft recovery and a talent to identify cause and effect. Often, their observations would prove invaluable to accident investigators.
While most of ASOD’s recoveries involved general aviation aircraft, they were also called upon to manage recovery of larger accidents, including the Delta L-1011 crash in August 1985 at Dallas/Fort Worth International Airport and the 727 accident there three years later.
Their stories often had that Texas touch of legend among those in the aviation community, but were just another day’s work for the crews. However, their main business was parts.
While retrieval was an invaluable support operation, it required borrowed manpower and equipment that took time and resources away from ASOD’s parts business. A few years ago, Camp decided to get out of the pickup and delivery business and created a separate operation dedicated solely to aircraft retrieval. He and Richard Ball, a former employee and recovery expert, set up Lone Star Retrieval. The move proved synergistic. ASOD was able to free its assets and concentrate on its core business, and Lone Star hit the road running and has been profitable from day one.
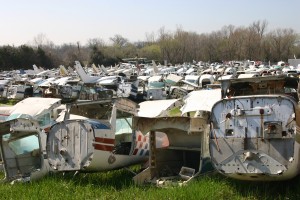
The back lot at Air Salvage of Dallas not only offers hundreds of damaged aircraft, but also provides a somber study in aviation safety.
The insurer usually makes initial contact for retrieval. As a totally independent business, Lone Star isn’t obligated to deliver the aircraft (or, in some cases, the car, truck or industrial vehicle) to Air Salvage, although it does in a majority of cases, because of the accident investigation facilities located there.
Facilities for accident investigation
Part of the acreage at Air Salvage isn’t open to the public. This area contains aircraft that are in litigation or under investigation by the National Transportation Safety Board. Typically, investigators have to work in crude and uncomfortable surroundings, often outside, so when ASOD built its new facility, a number of specialized locations were included, along with access to shops. Heated and air-conditioned hangars and shops are made available, along with conference rooms and accident reconstruction areas.
“We’re a neutral facility,” he said. “We don’t favor one side (of litigation) or the other, and we want to stay that way. In the past, we’ve been deposed, but with a volume of 100 to 120 airplanes brought in to be stored for investigation each year, we simply can’t remember all the details of each one, so we tell the truth: ‘I don’t recall.’ Most attorneys have come to respect our stand.”
Interestingly, the facilities have attracted the attention of the auto community as well. For the past few years, an increasing number of cars, trucks and other transport vehicles involved in litigation have been brought to ASOD for secure storage and inspection.
How to buy used parts
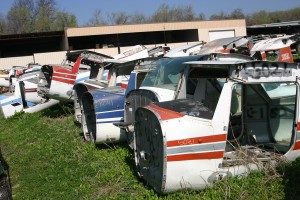
Aircraft are filed by model in neat rows and systematically provide useable parts and assemblies. When there’s nothing of value left on the airframe, it’s sent to a smelter to be recycled.
Most sales come to them over the Internet. Camp says they do business throughout the world, with the largest numbers of customers in the Philippines and South America. In many countries, customers use the Dallas operation not because of cost or convenience, but because ASOD may be their only parts source.
“Customers can buy parts two ways,” Camp explained. “We can drill the part out of an assembly and send it, or we can take a power saw and cut out the part and some of the surrounding metal. The second way means that the customer can save money by drilling it out himself, instead of paying us to do it.”
Because ASOD can sell with genuinely attractive prices, avionics generate a great deal of interest from customers. Each unit is thoroughly inspected and bench tested before being put in stock.
Whether you need a part or are just curious, a tour of Air Salvage of Dallas is well worth your time. In addition to acres of airplanes—each one with a story—there’s a gallery of photos of the company’s retrievals over the last 33 years on display in the offices.
For more information, call 972- 227-1111 or email [http://www.asod.com].