By Marilyn Noble
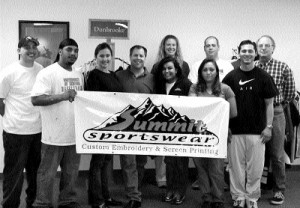
Dave LaPlante (center) and his experienced staff produce high quality shirts, jackets and caps for customers ranging from major corporations to local softball teams.
Summit Sportswear
The year was 1984, before the term “March Madness” was synonymous with NCAA basketball and when the Final Four was merely another college sporting event. Merchandise was limited to the usual school sweatshirts and the hot dogs and beer at the concession stand.
Dave LaPlante and some of his buddies found themselves at that year’s championship game, dubbed “The Battle in Seattle.” Patrick Ewing and Reggie Williams led the Georgetown Hoyas while Akeem Olajuwon and Clyde Drexler fronted an offense for the University of Houston, known affectionately by their fans as “Phi Slamma Jamma.”
“Everybody loved to hate Georgetown,” recalls LaPlante, “and the Houston fans had these great Phi Slamma Jamma t-shirts. We looked all over for them, but you couldn’t buy them. The only ones around were the ones people brought with them from Houston. It was at that point I said, ‘I’m gonna start a t-shirt business.'”
LaPlante kicked the idea around for another four years while he worked as a credit manager for Zenith Electronics, until one of his friends called him with an order for 400 t-shirts.
“He told me it was time to put up or shut up, so I took the order and got into the business,” says LaPlante.
After starting out as a broker, he and his wife, Christine, eventually bought their own equipment, and today, Summit Sportswear, headquartered in Centennial, turns out thousands of screen-printed or embroidered shirts, hats and jackets for everybody from large corporate clients and university athletic departments to the local Little League teams.
According to LaPlante, Summit is a full-service company.
“We sell the garments, do the fitting, and do the decorating, all in-house,” he says. “We know we can’t get all the business out there, so we’re very focused on quality. We give our customers a great product.”
And the customers appreciate it, not only by reordering products, but also by recognizing the company’s extra efforts with treats like homemade cookies for the staff.
“We’re lucky,” says LaPlante. “We have great customers all across the board, from small mom-and-pop companies to corporate giants like AT&T.”
He gives the credit for the quality of the company’s products to his employees. His two embroidery operators and the production manager have over 30 total years of experience in decorative embroidery, and most of the rest of the 11 employees have been with the company for at least a couple of years.
LaPlante and his crew can provide creative ideas for customers who aren’t sure what they want, and they’re willing to experiment with specialty inks and printing processes to create unique garments. Stacey Lane, Summit’s full-time graphic artist, can take a basic idea and turn it into a wearable work of art.
The company has three, six-head embroidery machines and an automated printer, but much of the work, like trimming and some of the screen printing, is still done by hand.
One of Lane’s favorite projects has been working with the students in the life skills program at South Middle School in the Aurora Public School District. One of the students in the special education program designed the artwork for this year’s t-shirt, and Lane has helped him refine it until it’s become an eye-catching statement.
Lane also enjoys a high-profile challenge. For the past two years, Summit has created t-shirts for “Bike to Work Week,” and for this year’s shirt, she had to reproduce a watercolor by local artist Barbara Froula.
“That was tough, getting all of the colors bright enough,” she says.
“But it was great,” adds LaPlante. “We have lots of fun with those kind of projects.”
In fact, fun is an unexpected side benefit LaPlante has experienced in his business.
“I think the one thing that has surprised me more than anything else is how much fun it really is,” he says. “People get excited to see their stuff, and it’s just great.”
Summit Sportswear is located at 6200 S. Troy Circle, Suite 220, in Centennial. For more information, call (303) 858-0060.
Global Air Response
They’ve transported movie stars, professional athletes and heads of state, but most of their passengers would probably rather be anywhere else than in one of the company’s specially outfitted Lears. Global Air Response is the largest air ambulance service in the country, having flown over 25,000 medical missions around the world in the past 16 years.
“Because of our worldwide ops specs, we’ve flown to every continent except Antarctica, and just about every country, with the exception of Libya and Yemen, because nobody can fly there,” says Dennis Rommel, company president and CEO.
Unlike many air ambulance brokers that contract for services with operators and medical personnel, Global Air Response operates under its own Part 135 certification, carries both medical and aircraft liability insurance and employs all of the medical staff and flight crews. According to Rommel, his captains have an average of about 5,000 cockpit hours each, with much of that experience coming over water and in international airspace. Chief pilot Keith Butler has about 14,000 flying hours, and Kevin Burkhardt, chief of operations, has logged over 12,000.
“All of our pilots are trained to flight safety, and we have our own check airman,” said Rommel. “Because of the places we fly, our pilots need to know lots of little tricks, like when to have an extra hundred bucks on hand to help things along at a foreign airport. Our captains have tons of international experience.”
Rommel believes in hiring locally, so most of the company’s copilots have come out of Centennial Airport flight schools. The members of the medical staff are also highly experienced and credentialed professionals. All of the eight full-time nurses have at least five years of hospital intensive care experience and receive recurrent training in flight physiology, flight safety and emergency medicine, as do the respiratory therapists who accompany some of the more critically ill patients.
“There’s no typical trip, which is the best part of the job,” says Jane Burkhardt, the company’s medical/legal coordinator. “Our patient population is so varied. Patients going to the Mayo Clinic for transplant evaluations need a higher level of care than most, but about one-third of our patients are not all that sick; they just need a medical transport that the commercial airlines can’t manage.”
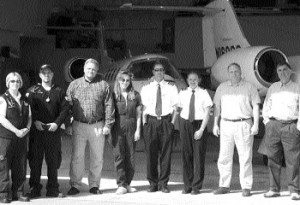
L to R: Global Air Response team members Devon Jensen and Drew Shaw, Action Care Ambulance; CEO Dennis Rommel, Jill Haradon, Tony Brotherton, Chrissy Baski, Dave Rommel and Tom Cox.
And because a patient’s condition can change while the plane is in the air, each aircraft carries a book of protocols developed by the company’s medical director, giving the flight nurses standing orders to deal with a wide variety of problems.
“We carry all kinds of comfort meds for pain and nausea, as well as cardiac meds and a ventilator,” says Burkhardt. “We can even intubate in the air if necessary.”
Each of the company’s four Lear 30 series aircraft has been outfitted like a small emergency room with a stretcher that has its own independent oxygen and power supplies, as well as monitors, infusion pumps, a ventilator and drug and supply packs. The planes can fly at an altitude of 40,000 feet, which gives a more comfortable ride and greater fuel efficiency, with a range of about 1,200 miles. The only thing lacking? A restroom.
“To get the stretcher into a Lear 35, you have to remove the bathroom that’s located behind the copilot’s seat,” says Rommel. “It can get pretty uncomfortable for the crew and family members if we have them along as passengers. But that’s about to change.”
Global Air Response just acquired a long-range Lear 55 that will carry two stretchers and has a rear lavatory. With a six-and-a-half-hour range, that’s an important amenity. The aircraft is also fully Reduced Vertical Separation Minimum compliant, allowing it to fly at optimum altitudes in European and Pacific airspace. And with its 1,215-gallon fuel capacity, the 55 will be able to fly non-stop between the West Coast and Hawaii, a trip that usually requires a leg north to Alaska and then south across the Pacific to avoid the prevailing trade winds and to allow for a refueling stop.
“I’ve been trying to get this 55 for two years now, so this is very exciting,” says Rommel. “This will mean we can fly non-stop to so many more places. It’s a really big deal for us.”
While Global Air Response has grown to become one of the most successful air ambulance services in the country, rising fuel costs and liability insurance premiums are creating concern across the industry. The company intends to focus on building and keeping contracts within its niche markets—major hospitals like the Mayo Clinic and Craig Hospital, major insurers like Aetna, organizations like the NFL and certain government agencies.
“This isn’t a lucrative area of aviation, and we run on really tight margins,” says Rommel. “But we save a lot of lives, and that’s what makes it worthwhile.”
Global Air Response is located at Centennial Airport at 7211 S. Peoria, Suite 200. For more information, call (800) 631-6565 or visiy [http://www.airresponse.net].