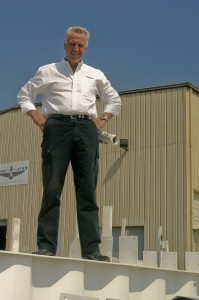
Jerry Curtis is on top of the world and on top of one of his “wavy-web” trusses. The innovative design allows for tremendously increased open spans in large buildings.
By Jeff Mattoon
When looking at Jerry Curtis’ invention, the prevailing thought is, “Why didn’t I think of that?” The concept is incredibly simple, yet incredibly powerful—literally.
Curtis’ company is EagleSpan Steel Structures, LLC. His product is an extraordinarily strong reiteration of the steel I-beam, an all-important support component in countless commercial and private buildings—particularly those requiring large interior open spans.
The design simplicity of many inventions is startling. With any steel I-beam, there are only three parts: a bottom plate or flange, a top flange and a vertical piece connecting them called the web.
I-beams are very strong, since they must support enormous weights, but, as with most construction components, there’s an Achilles heel—the longer an I-beam, the easier it will twist or torque. This is problematic when erecting a large structure, because the process of lifting and placing a beam takes extra attention and manpower to ensure the beam stays straight. If a beam is torqued too much while it’s being installed, repairs and replacement can become expensive.
When building with I-beam or “red-iron” trusses, another consideration is that of total span. There’s a limit to the distance I-beams can traverse before requiring the use of vertical support members. In a structure with huge open spaces, such as a large aircraft hangar, support posts in the middle of the floor will most certainly limit the maximum possible potential of that building.
One way architectural engineers have increased the open span of I-beam-constructed buildings is to beef up the size of the web. The obvious limitations of increasing the web’s size are the amount of steel it takes to support a large structure, and how that steel intrudes on the interior of the building.
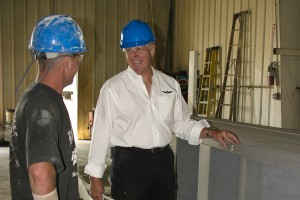
Superior quality is a top requirement for EagleSpan. Jerry Curtis (right) discusses a finished beam with Mark Dodson, production paint line manager.
To reduce this intrusion, at least near floor level, engineers designed tapered I-beams, which look like a triangle, sitting on its point with the widest portion high above ground. To gain the most possible interior space, it’s common for these outside perimeter support columns to be placed inside the building, requiring the designer to leave them exposed or to finish them with drywall, plywood or some other material. It may ultimately look fine, but the support member gobbles up a good bit of useable floor space.
A series of events would lead Curtis to come up with a better solution.
Life takes funny turns
Curtis acknowledges that many of his experiences have placed him in an incredibly fortunate position, allowing him to capitalize on unfulfilled needs.
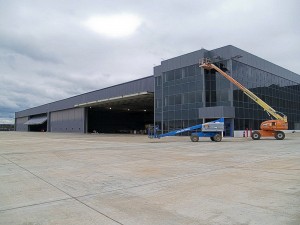
The newly completed Dulles Jet Center is one of many crown jewels in the EagleSpan collection of large, open-span aviation buildings. While the Jet Center isn’t the largest clear-span building for EagleSpan, it’s the current overall largest at over 1k ft.
As a teenager, he worked in a uranium mine, learning the value of a hard day’s work. He moved to Colorado from Oklahoma in the mid-1960s to attend college, aspiring to be an airline pilot. By the late 1960s, he had all the ratings needed for the airlines, including his commercial, multi-engine and CFI. All he needed was a college diploma.
To support himself, his wife and one small child, he worked at an appliance store selling and repairing. There, he met a banker from across the street who offered him a job selling banking software. Curtis jumped at the chance. Within 30 days, after the bank found out he was a pilot, he took on the new role of corporate pilot. He never did return to college.
Using the knowledge he learned at the bank, Curtis later entered the oil and gas wholesale business, teaching investors how to purchase securities.
The fortune he made allowed him and his wife at the time, RaeAnn, to get involved in ranching and participate in equestrian dressage. An incident involving one horse would lead to the formation of EagleSpan.
Horse hips and iron are bad companions
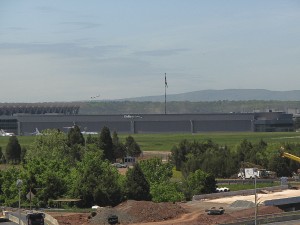
A panoramic view of the Dulles Jet Center shows the adjacent General Dynamics building, also equipped with the unique EagleSpan trusses.
Curtis explained that it takes eight to nine years to get a dressage show horse to the Grand Prix level. In 1991, they had a horse that was at that level.
“His name was Bailey’s Best, because he was the color of that Irish crème beverage,” Curtis recalled. “He was a wedding present and he was beautiful. We were spending a fortune on training, feeding and shoeing.”
At an event the couple attended with Bailey’s Best, in an arena not suited for horses, a serious and unforeseen accident occurred. While making his rounds in the arena, the horse clipped the side of an exposed vertical I-beam, shearing a bone at the hip.
“We were a thousand miles from home, so we had to bring this horse back in a trailer,” recounted Curtis. “It was painful.”
Bailey’s Best survived the incident, but Curtis knew there had to be a better way to build horse arenas. Shortly after that, a friend invited Curtis to lunch and introduced him to Australian Ian Barryman. During the conversation, Barryman revealed he had invented a way to manufacture trusses that allowed much longer spans with less steel than typical red-iron construction.
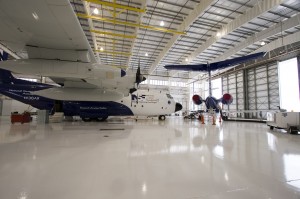
EagleSpan projects include the University Corporation for Atmospheric Research’s 35k square-ft hangar at Rocky Mountain Metropolitan Airport, which houses the NSF/NCAR High-performance Instrumented Airborne Platform for Environmental Research and a C-130.
The Australian builder had changed the web component of a steel I-beam. Instead of a straight piece of metal running the length of the beam, he put a “wave” in it, creating something similar to a corrugated box. By adding a wave to the web, structural strength increased exponentially, allowing both huge spans and a reduced amount of steel needed for each truss.
“It got my attention,” Curtis said. “The minute I looked at those pictures, I saw in my mind the solution I needed.”
He had the time and the money to investigate Barryman’s invention, and as a do-it-yourself, hands-on kind of person, this was something that strongly piqued his interest. Shortly after meeting Barryman, Curtis boarded an airplane heading to Orange, 160 miles west of Sydney.
“I kind of did it on a lark,” he recalled. “I really wanted to see it. I was so intrigued by the idea, because I hadn’t seen anything like it.”
When Curtis returned to the States, he still hadn’t made the decision to start a new company, but he began to discuss it. One person he spoke to was Chuck Long.
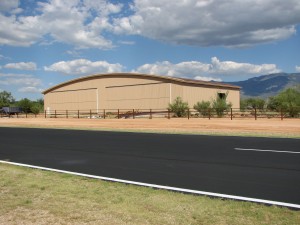
A private hangar in Tucson, Ariz., is currently EagleSpan’s largest curved-roof clear-span at 150 feet.
“I was looking at his daughter’s horses and telling him about it,” Curtis said. “I said, ‘Chuck, you should see this beam I saw in Australia.’ I explained how it could span long distances. Like myself, he said, ‘I’ve got to see it.’ I pointed out that it was in Australia, but he said, ‘I don’t care, let’s go.’ And we did.”
Soon after their casual conversation, the two headed to Sydney. While sharing their enthusiasm about the new truss building method on the plane ride back, Long asked Curtis if he thought he could use the idea to build an 80-foot bridge. Of course, Curtis said yes.
A waffle-stomper and the Atlanta Olympics
To build that bridge, Curtis had to first hand-build the “waffle- stomper,” which would be used to build more bridges and Curtis’ first building. And it didn’t stop there.
“I built $11 million worth of buildings on my prototype,” he said. “It was a success; we ended up using it from day one.”
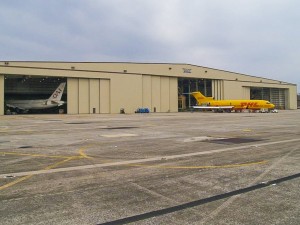
The Flight Star aircraft modification facility in Jacksonville, Fla., is EagleSpan’s current largest clear-span building at 648 feet by 240 feet. The company is currently working on a building in Singapore that will offer much larger clear-span dimensions
With the help of Chuck Long paying licensing and patent fees, Curtis was in business—almost. As the “business” was coming together, Curtis wasn’t sure he wanted to jump in with both feet.
“I was at the 1996 Olympics in Atlanta,” he remembers. “I was talking to Chuck on the phone and he said, ‘You really ought to go ahead and do this thing if you’re going to do it.’ I said, ‘Chuck, I’m just not sure.’ Then, while we were down there, we ran into a friend of my wife’s. After we spoke about what I was doing, she said, ‘If you’ll start this company, I’ll buy your first building.'”
It was EagleSpan Steel Structures’ first official order: a private horse arena in Prescott, Ariz. The equestrian industry is tight-knit, and in a short time, EagleSpan was providing “waffle beams” for dozens of projects.
The EagleSpan beam is easy to spot because of it wavy web feature, but it also has another distinction.
“Part of the service I offer with my buildings is that they’re all painted white,” says Curtis. “I put on five and a half mils of paint, whereas the average manufacturer puts on one and a half mils. They just throw it on, as cheap as they can get, because that’s not part of the finished process. Very often, when our trusses go up there’s no need for paint, because it’s done already.”
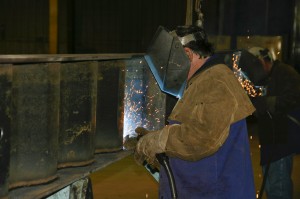
Welders attach the “wavy-web” to the bottom flange. Every EagleSpan truss is custom made for each installation.
The inspiration to paint all trusses white came, again, from horses.
“Using white and creating large, open, bright spaces is totally by design,” said Curtis. “Horses are creatures of flight. In their minds, if there’s a dark area in the space, it means there’s a lion or tiger in there; every dark spot hides something that’s out to eat them. Consequently, I applied this understanding of how they think to those arenas to begin with. Horses in my buildings are relaxed; they’re calm, because there’re no dark spots.”
From horses to airplanes
From bridges to commercial buildings to horse arenas, Curtis’ path eventually wound its way to aviation. Today, 86 percent of the corrugated I-beams EagleSpan creates are for aviation clients. Regardless of size, all components are custom manufactured. For Curtis, there’s no such thing as cookie-cutter.
Completed aviation projects include small private hangars as well as the huge Dulles Jet Center at Washington Dulles International Airport (IAD) and the adjacent General Dynamics facility.
The company recently introduced a product line of EagleSpan hangar doors. For years, Curtis felt frustrated with the lack of workmanship and the failure rate of many of the hangar doors he encountered. For the two-and-a-half-year period his company has manufactured its hangar doors, there hasn’t been one failure. According to Curtis, it’s due to the workmanship of the product.
“It’s our calling card,” he said. “While other companies seem to cut corners, I look at it a little differently. I’m not afraid to put better products in the door. Like latches, for instance; I don’t have any mechanical latches. Electronic actuators open the door. You push a button, and you open the door from the outside. It’s all electronic.
“And that’s a superior quality in the door itself. We use Baldor motors—the best motors you can buy. They’re direct drive; the transmission is super quiet.”
He said he knows that EagleSpan’s doors weigh more than anybody else’s.
“You have to build strength into a door, because they’ve got to withstand tremendous pressure from wind and repeated use,” he said.
What’s ahead?
In just a decade, EagleSpan has become a global business with an average 20-plus percent growth rate, thanks in large part to the Internet. Curtis is rightfully proud that the company has only had two cancellations in its history.
“One of those was bought by the truck driver who delivered the refused shipment,” he said. “With the other one, we received a down payment, but the purchaser couldn’t afford it.”
The events of Sept. 11 affected EagleSpan. In the following months, the company received no new orders. Fortunately, Curtis was able to weather the storm, due to a tremendous backlog. In subsequent years, material costs rose tremendously, but Curtis fulfilled every order, on time and at the price quoted.
What’s on the horizon for EagleSpan? Curtis revealed that the company is working on numerous large-scale global aviation facilities. One of those projects is the manufacturing facility for a soon-to-be-announced supersonic jet built in Singapore.
Curtis obviously had the right idea when he made that journey halfway around the world on “a lark.”
For more information, visit [http://www.eaglespan.com].