Not long after James Raisbeck left Boeing and became involved in general aviation, he noticed something that was disconcerting.
“In its history, the entire general aviation industry has lagged behind the commercial and military aviation business in technology,” he said. Raisbeck didn’t just recognize the problem; he realized he had the ability to see “gaping holes” in the industry’s technology. And once he saw those gaps, he knew he’d have to search diligently for ways to bridge the chasms. That led to Raisbeck’s lifetime goal: breathing new technology into currently flying airplanes. Since the 1970s, he has indeed breathed new life into various aircraft, through Raisbeck Commercial Air Group and its parent company, Raisbeck Engineering. The Seattle-based aeronautical engineering firm designs, engineers, flight-tests, certifies and manufactures systems that increase productivity and safety on business and airline aircraft. More than 4,000 business jets and turboprops are flying with Raisbeck Systems, sold and installed worldwide through a network of Raisbeck Engineering dealers. Raisbeck’s products are also on the Hawker Beechcraft King Air production line in Wichita, Kan. His influence on the face of aviation is the reason Airport Journals named him the 2007 Living Legends of Aviation Lifetime Aviation Entrepreneur. Although many people try to forget their missteps along the way, Raisbeck appears to embrace them. |
|
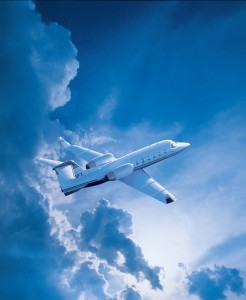
Raisbeck Engineering’s ZR LITE wing and flap system, installed on this Lear 31, reduces cruise drag by almost 10 percent and increases the FAA-certified takeoff performance, allowing airplanes to operate safely out of many previously unavailable airports.
“Every big point in my life was a lesson learned,” he recently told Kim Blonigen of King Air magazine.
In life’s classroom, he especially learned the importance of four things: picking a goal and sticking with it, learning from the masters, owning a piece of the action and carefully choosing business partners.
“Each of these lessons came from a mistake,” he said, adding that everyone makes mistakes, but the difference between winners and losers is that winners typically don’t make the same error in judgment twice.
Raisbeck also believes he’s found a surefire way to make sure he stays a winner.
“I’ve been fortunate to surround myself with intelligent, dedicated people—people who are in love with aviation and new technology,” he said.
“You can’t skate by at Purdue”
Raisbeck grew up in Whitefish Bay, a suburb of Milwaukee, Wis. Although it was the era of World War II, when many dreamed of becoming pilots, he had a passion for mechanical devices. In 1947, he designed, built and raced his car in the local Soap Box Derby.
“Following that, I built a quarter midget racer from scratch,” he said. “I crashed into a ditch on the first test drive, but learned a bunch about steering mechanisms.”
Although designing and making things work was a passion, school wasn’t.
“The only ‘A’ I got was in gym; I had to do that for football,” he laughed. “I just slid through.”
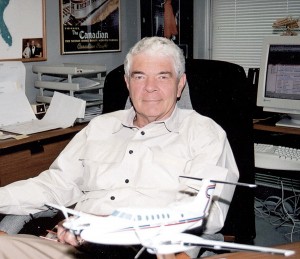
Since the 1970s, James Raisbeck has breathed new life into various aircraft, through Raisbeck Commercial Air Group and its parent company, Raisbeck Engineering.
After high school, Raisbeck enrolled at Purdue University. He entered the institution in 1954, with the mission of studying mechanical engineering. However, he lasted only one semester before a rude awakening.
“I flunked,” he said. “You can’t skate by at Purdue.”
But Raisbeck had set a goal. He optimized his commitment to engineering by joining the Air Force. Part of the reason he enlisted was that he had dug himself deep into a hole, including the revelation that he was facing fatherhood. The military would offer him the discipline he knew he needed.
“I joined the Air Force as an E-1,” he said. “I had to find a way to support my wife and daughter. I wound up all right over the four years active duty. I became a flight engineer.”
As a mechanic and flight engineer, he gained the experience that would later become his muse.
“That experience taught me that knowing systems is as important as knowing how to fly,” he said.
After his four-year enlistment in the USAF was over, Raisbeck returned to Purdue University, in 1958, to more successfully complete his studies.
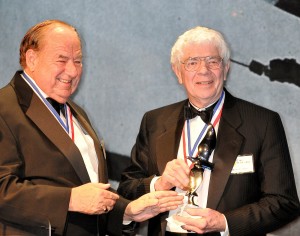
Airport Journals named James Raisbeck the 2007 Living Legends of Aviation Lifetime Aviation Entrepreneur due to his influence on the face of aviation. Clay Lacy, the 2004 award recipient, presented the award.
“The GI Bill wasn’t enough to cover the costs of tuition and living expenses, so I signed up for active reserve duty with the 434th Troop Carrier Wing at Bakalar AFB, Columbus, Ind., as a flight engineer,” he said. “We logged three day’s pay every weekend, flying somewhere for training or on supply missions. I did my calculus homework on the radio operator’s table, glancing occasionally at the instruments while in flight.”
Raisbeck received a degree in aeronautical engineering, science and mathematics.
“Since then, I’ve taken everything to do with airplanes—aeronautical engineering, airflow, fluid flow, systems, anything to do with the industry and the supporting technology—and stored it in my head for possible future reference material,” he said.
Learning from the masters
In 1961, Raisbeck joined Boeing as a research aerodynamicist. He quickly realized the opportunity he was given to associate himself with the “masters” of the business and acquire knowledge from them.
His first boss was Bernie Gratzer, head of Boeing’s aero research group (who would, after retirement, join forces with Joe Clark at Aviation Partners Inc., resulting in their blended winglet).
While with Boeing, Raisbeck and a team of engineers and flight crew designed and flight-tested an internally blown trailing edge flap system on the prototype 707, 367-80, known as the “Dash 80.”
In order to test the response characteristics of an alpha/beta airflow sensor in an economical way, Raisbeck offered up his 1962 Jaguar XKE. After running up and down Boeing Field at speeds to 120 knots in 1963, the recorded data was fed into the computers aboard the DASH 80, when the same instrument was mounted on a nose boom 30 feet in front of the aircraft.
In December 1963, the DASH 80 lifted off the runway at Boeing Field and into the history books as the world’s slowest-flying jet transport. The airplane flew regularly at speeds as slow as 60 knots, at gross weights exceeding 150,000 lbs. The inventions and aerodynamic insights from that and other similar programs became the basis for low-speed configurations of subsequent Boeing model airplanes. Today, the DASH 80 resides in the Smithsonian Air and Space Museum at Washington Dulles International Airport.
Other assignments at Boeing included liaison with the aeronautical laboratories at Wright-Patterson AFB and designer/program manager in preliminary design.
“They gave me plenty of rope—so many hard problems to figure out,” Raisbeck said. “That’s my passion.”
While he worked there, he took another step into the aviation world. He took flying lessons.
Might as well own it
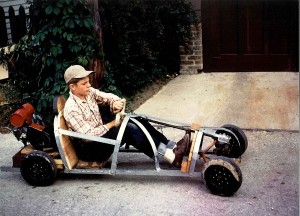
After designing, building and racing his car in the local Soap Box Derby in 1948, 11-year-old James Raisbeck built a quarter midget racer from scratch.
Raisbeck left Boeing in 1969 for Robertson Aircraft Corporation in Seattle. That position eventually resulted in his placement as chairman, CEO, president and chief engineer.
There, he and his team completed the Robertson STOL (short takeoff and landing) designs and certifications for single- and twin-engine Cessnas and Pipers.
Raisbeck recalled that the company got needed exposure when Cliff Robertson arrived at the office one day, asking if he could borrow a Robertson STOL airplane to use in “J.W. Coop,” a movie Robertson was starring in and directing. Seeing a great opportunity, Raisbeck supplied the actor-pilot with a Robertson STOL Cessna 207.
“After the movie came out, we made three additional sales—and were able to make the payroll,” Raisbeck said.
While designing and certifying a STOL version of the Cessna 421 in 1971, one element of that system was the 100 percent chord Fowler flaps, uniquely designed and manufactured using composites.
“Some of the techniques we used in those days to understand airflow were rather crude by today’s standards, but they were effective, nevertheless, and gave us answers to help in our development work,” Raisbeck said.
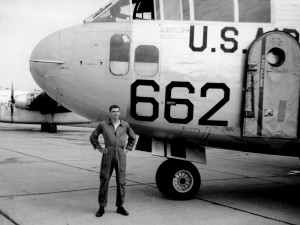
While attending Purdue University in the late 1950s, James Raisbeck earned extra money by extending his Air Force tour to include Reserve flying as a flight engineer on Fairchild C119s.
In 1973, after it had expanded, Robertson Aircraft was sold. It was time for Raisbeck to reevaluate his life. While working briefly with Al Paulson at American Jet Industries in Los Angeles as vice president of technology, he came to the realization that if he was going to work seven days a week, he should paint his own name on the hangar.
Careful choices
Raisbeck founded Raisbeck Engineering in 1973, on his dining room table, with $500. He says the core of his company was based on the ability to conceptualize and fill the “perceived and real needs” of customers.
“You don’t have much going for you long-term unless you can do that,” he said.
Today, his major focus remains on doing that, in a creative, unique way, through aerodynamics.
“The word itself is intangible,” he said. “Aerodynamics leads the forefront of technology and is the least understood. It’s a largely invisible concept to understand.”
The company got off to a good start, tasked with redesigning the Learjet’s wings for Gates Learjet in 1974.
“They wanted us to reduce the approach and takeoff speeds of the Learjet family,” he recalled.
That year, Clay Lacy had introduced Raisbeck to Dee Howard, founder of Howard Aero and The Dee Howard Company. In the early 1960s, Howard had built the mock-up of Bill Lear’s first jet and certified the Howard 250, 350 and 500 piston business twins. As Raisbeck worked on the Learjet Mark II development, Howard was building engine thrust reversers for Lear’s aircraft family.
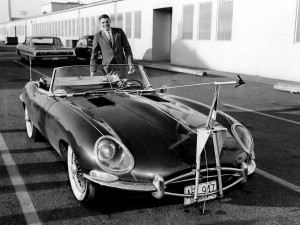
In 1963, when Boeing was testing an internally blown trailing edge flap system on the Dash 80, James Raisbeck’s 1962 Jaguar XKE ran up and down Boeing Field at 120 knots for economical testing of an alpha/beta airflow sensor’s response characteristics.
“When we met, Dee said, ‘If you ever have a problem completing that Learjet contract for one reason or another, you just come on down to San Antonio, and I’ll help you out,'” Raisbeck remembered.
In February 1975, Gates Learjet gave Raisbeck the opportunity to take Howard up on that offer.
“I came limping into San Antonio with no money in my pocket, but a few well-bent pieces of aluminum,” he said. “Dee backed it on the spot, and we became partners.”
They would also become lifelong friends. Howard recalled his desire for Raisbeck to be successful.
“What he was doing to the Learjet to make it stall slower would also help it to perform better, but he wasn’t making the progress that was expected,” Howard said. “We wanted to help him complete the terms of his agreement. I made a deal with Harry Combs to bring the test airplane and Jim to San Antonio to finish the program.”
Gates Learjet adopted the Mark II wing’s principles in 1976. The system’s enhancement of the low-speed Learjet flight characteristics and short runway performance led the Learjet factory to adopt the highly successful technology on new production aircraft. The work with Learjet also led to a contract with Rockwell International.
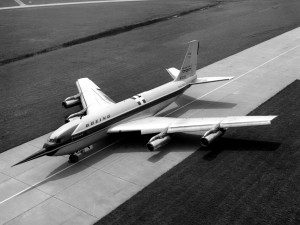
The DASH 80 prepares to fly with the nose boom, sensors and high-lift systems installed. Even the horizontal tail had upside-down leading edge slats for high negative tail lift. The airplane flew regularly at speeds as slow as 60 knots.
Rockwell asked Raisbeck to redesign its Sabreliner series in 1976. All production Sabreliner 65 aircraft would be equipped with supercritical wings, and Sabreliner models 60 and 80 would be retrofitted. Raisbeck again went under contract, this time with Rockwell.
“Rockwell asked us to work on reenergizing the Sabreliner program,” Raisbeck said. “We had a successful, technical piece of equipment in the Mark V wing, the first supercritical wing in service in the United States, but we couldn’t get it through their corporate.”
When Bob Hoover, at Rockwell’s North American Aviation Division, heard about the problem, he volunteered his help.
“He said, ‘Let me have a crack at that airplane,'” Raisbeck recalled. “When he came back from flying it, he said, ‘Jim, that’s a pretty darn good wing; I think we should push it through for the new Sabre 65,’ which is what happened.”
Raisbeck built all 75 wing sets for the Sabre 65 in Seattle, and shipped them to Rockwell in El Segundo, Calif. He now had 750 employees, most working on the supercritical wing. Although the program was a technical success, by 1979, Raisbeck’s company was in financial distress.
“The financial arrangements were a bit one-sided. Rockwell provided me with the ‘opportunity’ to start all over!” Raisbeck quipped.
The experience brought him to the realization that one has to choose business partners carefully. He also learned that bigger isn’t necessarily better.
“It’s sort of like sleeping with an elephant,” he said. “It’s great ’til she rolls over.”
Starting over
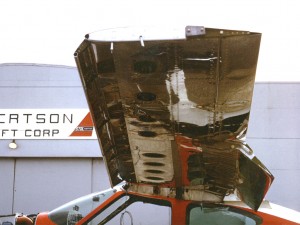
In 1970, Robertson Aircraft built advanced wings for the Cessna Cardinal in cooperation with Kansas University and NASA. They featured movable leading edge devices, Fowler flaps and spoilers for roll control. The airplane was successfully flight-tested.
Raisbeck regrouped and reformed his company in 1981, keeping five employees. He retained the basic overall engineering and conceptual design direction and flight-testing of performance improvement packages, but began using outside sources for detailed part design and production.
“I started operating under a new standard, to fill Raisbeck Engineering’s facilities with card-carrying experts, across a broad technical field, who know how to take responsibility and who can identify consultants and guide and monitor them,” he said. “We still operate that way today.”
At Raisbeck Engineering, located adjacent to Boeing Field, “hard-core experts in their field work together, like the stops on an organ.”
“I’m the organ player,” Raisbeck said. “My job is to push and pull the stops to make the music sound right.”
Raisbeck says the ideal airplane is an exquisite compromise of mission-driven requirements. When searching for aircraft in need of innovative technology, he looks for a group of aircraft that are generally popular and preferably still in production. Beechcraft’s King Air series fit that description perfectly.
In 1981, as Raisbeck Engineering’s executive vice president, Joe Clark, a fellow aviation entrepreneur, would be at the center of a transaction that would unite Raisbeck with the King Air.
“Joe’s the world’s best dealmaker,” Raisbeck said. “He fixed up a deal with Morrison Knudsen and got us going on the King Air in 1981.”
Getting back to the theme of the lack of change in aviation over the decades, Raisbeck points to the Bonanza, which came out in 1947. He compares it to the Beechcraft Queen Air, which debuted in 1958, and the King Air C90, certified in 1963.
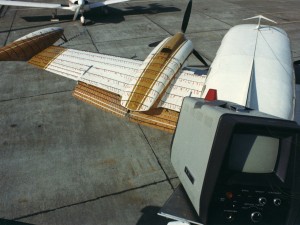
For the Robertson STOL Cessna 421, 100% chord Fowler flaps were uniquely designed & manufactured using composites. The flaps were tested for stall patterns using tufts for flow visualization. Note the period video camera 1971 mounted on the vertical tail.
“The Queen Air is a twin-engine version, in one form or another, of the Bonanza,” he said. “It has the same wings. The King Air is a turboprop conversion of the Queen Air. They have the same doors, same everything, except the King Air is powered by turboprops instead of piston engines.”
So, Raisbeck began developing a performance enhancement system for Beech Aircraft’s King Air family. Today, his relationship continues with the Hawker Beechcraft Corporation. Raisbeck systems are standard on Hawker Beechcraft’s Super King Air 350 production line and are factory options on its new production King Air C90GTI and B200GT models.
Raisbeck said that since the King Air models are all variations of each another, they’re generally the same in the areas that Raisbeck Engineering can improve, making it easier for the company to provide systems for new and existing aircraft.
“Relatively high production rates are then possible, which in turn justify expensive hard tooling,” he said. “That makes for great precision parts.”
For these performance enhancement systems, Raisbeck worked with the knowledge that synergistic effects increase overall performance and productivity of an airplane.
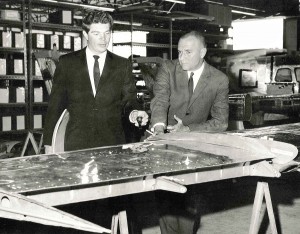
Reims Aviation President Pierre Closterman (right) and Robertson Aircraft Corporation President James Raisbeck review details of the Robertson STOL system being installed on the Reims Aviation Cessna 337 Milirole production line in France in 1970.
“On the King Air 200, for example, as part of the performance package for that airplane we changed out the wing inboard leading edges,” he said. “They were originally made from a combination of aluminum and honeycombed sandwich material, which tends to separate over the years due to heat, cold and moisture.
“We also reshaped the aerodynamics of those leading edges on that wing with composite material. The leading edges reduce the drag, and the airplane can fly faster at the same power. They also decrease the stall speed. We reduced the fuel consumption as well. And fuel reduction increases the payload and range. Achieving this by simply changing the leading edge of an airplane is truly fascinating.”
These, along with several other performance-improvement elements for the entire King Air family, make up Raisbeck Engineering’s EPIC Performance Packages.
In the 26 years Raisbeck Engineering has been providing systems for the King Air family, the company has never had an FAA airworthiness directive, mandatory service bulletin or causative accident. Raisbeck attributes that to his company’s strict attention to detail, ultraconservative structural design and constant customer follow-up to track service life.
Recent numbers show that more than 2,500 King Airs have at least one of the Raisbeck systems installed.
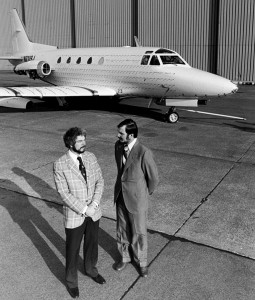
James Raisbeck (left), with Kim Frinell, vice president of flight test and engineering, used this prototype Sabreliner to develop the Mark 5 supercritical wing in the 1970s. The “hairs” on the airplane—tufts of yarn—are for in-flight flow visualization.
Raisbeck Engineering has also teamed with engine modifiers. Blackhawk Modifications is one such company. Together, they offer King Air owners a joint program incorporating higher power, factory-new Pratt & Whitney engines and the full Raisbeck EPIC Performance Packages. The company works with Hawker Beechcraft to be certified in parallel with new versions of various King models.
Raisbeck Engineering also recently upgraded and enlarged its nacelle wing lockers, which add storage space outside the cabin, making room for more passengers.
The King Air family additionally benefits from Hartzell/Raisbeck Quiet Turbofan Propellers, which dramatically reduce cabin and community noise and increases takeoff performance, while allowing for increased takeoff gross weight. Raisbeck has been designing and certifying propellers with Hartzell since 1983, incorporating uniquely optimized blade airfoils and other aerodynamic properties, which contribute to better overall performance and vibration-free flight from takeoff to touchdown.
Continued relationship with Learjet
For more than three decades, most Learjets have sported Raisbeck wings. Innovations have included the Mark II and Mark IV wings for the Lear 20 and 30 series, now standard technology on these models and called Century III and Softflite wings.
In 1994, Raisbeck introduced the aft fuselage locker for 31/35/36 Learjets, carrying up to 11 cu. ft. and 300 lbs cargo with easy external access to the watertight locker. Another plus is further reduction in drag. The locker went on the Learjet production line and is currently sold as a retrofit.
Raisbeck continues an ongoing technological review of the Learjet family; his recent goal has been to reduce cruise drag at typical cruise Mach numbers by a minimum of 10 percent. The company’s Learjet drag reduction program is another in the continuing series of remarkable contributions made to the Learjet family by his engineers over the past 30 years.
Seattle businessman Bruce McCaw loaned Raisbeck his Lear 35 from 1993-1995, to develop the company’s aft fuselage locker. He also leased his Learjet to Raisbeck Engineering from 2002-2005, for the development and certification of the ZR LITE Performance Package.
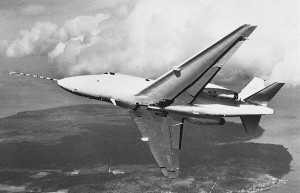
After Raisbeck was asked to redesign the Sabreliner series in the mid-1970s, Bob Hoover did some flight-testing to evaluate the supercritical wing. All production Sabreliner 65 aircraft were equipped with the wings, & many 60 80 models were retrofitted.
“We put 500 hours on it, developing the drag reduction system for the new 35 and then the Lear 31,” Raisbeck said. “Bruce only wanted to know when he could get his airplane back so he could remain current!”
The ZR LITE wing and flap system reduces cruise drag by almost 10 percent and increases the FAA-certified takeoff performance, allowing these airplanes to operate safely into and out of many previously unavailable airports. The Learjet 35/36 were first to be certified, in 2005, followed by the Learjet 31/31A in 2006. Bombardier Aviation Services and other independent Learjet maintenance facilities make these kit installations in the U.S. and internationally.
Current research and development projects underway include the expansion of the ZR LITE fuel-saving drag reduction systems for other business jets as well as aft fuselage fuel tanks, luggage lockers and avionics pods for the Learjet 55/60 Gulfstream GIV/GV and Bombardier’s Challenger 601/604 and Global Express family.
Boeing 727 noise reduction
Raisbeck Engineering has also been active in the world’s commercial airline fleet. In 1996, the Raisbeck Commercial Air Group completed recertification of the Boeing 727 to meet Stage 3 noise limits without weight and performance penalties.
The Raisbeck Stage 3 Noise Reduction Systems for the Boeing 727 covered all models and weights. Aerodynamic innovation provided Stage 3 noise compliance without costly engine modifications, saving their operators several million dollars on each installation.
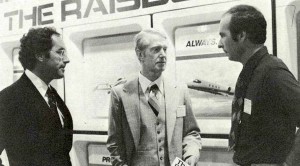
During NBAA 1977, Raisbeck employees Joe Clark (left) and Tom Wright (future chief test pilot on the Raisbeck 737 Stage 3 program) converse with Procter & Gamble’s director of aviation (center). The company bought 4 retrofit systems for its Sabreliner 80s
American Airlines ordered and took delivery of 52 Raisbeck 727 Stage 3 systems. Other customers have included TWA, Pan Am, Air Algerie, TAME and many smaller airlines. The systems are now flying on many of the remaining Boeing passenger and cargo 727s worldwide, including one for Clay Lacy, another aviator for whom Raisbeck has much praise.
Airbus A320 cabin efficiency
Raisbeck provided a redesigned overhead bin system For JetBlue’s fleet of Airbus A320s that resulted in more efficiency and room. August 2001 marked the first in-service date for Raisbeck’s A320 Family Overhead Bin Door Enlargement Kits.
Because of the design of enlarged bins, popular, 22-inch, upright bags carried by passengers could be stored crosswise, with the handle facing the door. The redesigned overhead door and extended bin floor almost double the usable overhead storage space, allowing for quick and easy baggage stowage. Raisbeck has now equipped all of JetBlue’s Airbus fleet of more than 100 aircraft.
Safety, performance and productivity
With safety constantly his top priority—followed by performance and productivity—Raisbeck began developing bulletproof doors and bulkheads for Boeing 737s and 757s in 2000.
Four weeks after the 9/11 tragedy, Alaska Airlines began installing Raisbeck’s prototype Hardened Cockpit Security System on its 737 fleet. Alaska Airlines, American Trans Air and other airlines operating the Boeing 737 immediately ordered and took delivery of the cockpit doors. The doors included rapid decompression, emergency pilot egress and crash-crew cockpit ingress, bulletproof protection, cockpit-to-cabin visual identification and structural integrity.
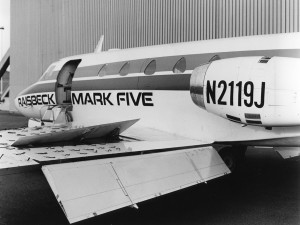
This prototype Sabreliner, with the Mark 5 supercritical wing, full-chord Fowler flaps and wing spoilers, deployed in final configuration for FAA certification in 1978.
Raisbeck began the certification process in October 2001, with the doors designed to meet or exceed all FAA requirements. With Raisbeck Engineering acting as a catalyst, the airline industry could focus on early and cost-effective solutions to the Federal Aviation Administration’s certified flight-deck security system requirements for April 2003.
When Boeing firmed up a program with an early delivery schedule to complete the retrofit of its fleet, Raisbeck was already delivering the only long-term FAA certifiable cockpit security systems available. In March 2002, Raisbeck turned over its flight deck security business and customers to Boeing.
“It’s far more important that the worldwide operators of Boeing aircraft enjoy the commonality of Boeing-designed systems in this critical area,” Raisbeck said about the decision. “We’re grateful to have been able to make an early and technically successful contribution to the Safety in the Skies airline program.”
Making it in the industry
Raisbeck says six factors are important to the success of his systems. The first five are payload, speed, range, accessibility in reaching airports and total operating cost. He explained that unless someone understands and contributes to these factors, the modification isn’t worth much to the owners and operators. The sixth factor is pure sex appeal.
“In the general aviation business, if it isn’t sexy, it’s not going to sell well,” he said.
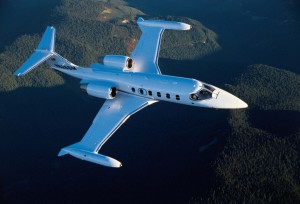
Pete Reynolds served as the project pilot while the prototype Raisbeck ZR system was tested on Bruce McCaw’s Lear 35 from 2002-2005. The inboard leading edge extensions weren’t retained in the developed, certified version.
When it comes to the idea of “success,” Raisbeck says he doesn’t feel that necessarily means being a big and wealthy corporation. He says that profits paid by happy customers internally generate 100 percent of his company’s R&D money. He believes that’s been possible because of some key business principals.
“First, when they’re coming up with a new product, don’t make any sales until that product is proven, certified and in production,” he said. “Then, and only then, can sales and deliveries begin. Marketing and sales cannot dictate an early and perhaps unsupportable delivery date. So, our company doesn’t make promises until it’s sure. Also, it’s important for everyone at Raisbeck Engineering to know our products, how they work and their value to the customer.”
He adds that the real relationship with customer really begins after the sale’s consummation.
“Then it’s service, service, service,” he said. “These are a few principles that make Raisbeck Engineering what it is today. And, if we have an in-service part that has a high replacement history, we identify what it is and why, and we fix it. We owe that to our customers.”
Service and acknowledgments
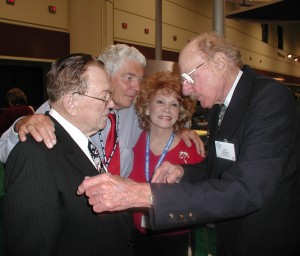
Betty Howard listens as Dee Howard (left), James Raisbeck and Bob Hoover talk over some of the more abhorrent flight characteristics of various prop and jet business airplane types they’ve been involved with over the years.
Raisbeck also finds ways to serve others outside his own business. He’s on the board of The Museum of Flight, the Seattle Opera, Pacific Northwest Ballet, Seattle Symphony Orchestra and The Seattle Arts Fund. In 2003, Seattle’s Hope Heart Institute honored Raisbeck and his wife, Sherry, an artist and former special education teacher, with its “Wings of Hope” annual award for their leadership in philanthropy.
The Raisbecks were selected as the 2007 Seattle-King County First Citizens for their generous support of local arts, education and medical research organizations. The couple was honored with the 69th annual First Citizen; the award was created in 1939 to honor the icons of philanthropy and community involvement.
The Raisbecks also travel with the Pacific Northwest Ballet while underwriting its international tours. They underwrite the lead singers at the Seattle Opera, in exchange for lunches with those singers. They sponsor guest artists at the Seattle Symphony.
Through their foundation, the Raisbecks matched $1.5 million from other donors for the Fred Hutchinson Cancer Research Center, resulting in $3 million raised during the 2000 Hutch Holiday Gala. The donation was used to open a new branch of cutting-edge lymphoma research at the center.
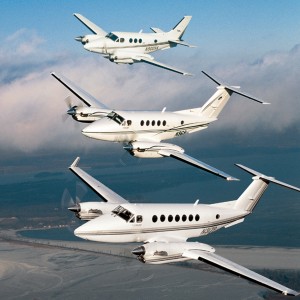
From top: A King Air C90, Super King Air B200 & Super King Air 350 make up a three-ship formation of Raisbeck-equipped King Airs. More than 5k of these King Airs are currently flying, forming the basis of Raisbeck Engineering’s successful retrofit program
The Raisbecks have also made a major gift for new educational facilities at Seattle’s Cornish College of the Arts. Other grants have gone to Purdue University for scholarships and research, and to endow a distinguished engineering chair. Raisbeck additionally established the Raisbeck Engineering Distinguished Lecture Series at Embry-Riddle Aeronautical University.
Raisbeck’s hard work and talent haven’t gone unnoticed. Purdue University honored him with its Distinguished Engineering Alumnus Award in 1979, and two decades later, presented him with its Outstanding Aerospace Engineer Award. Also in 1999, the American Institute of Aeronautics and Astronautics, where he is an associate fellow, honored him with its Commercial Aviation Technical Achievement Award.
In 2000, Professional Pilot Magazine named Raisbeck Aviation Entrepreneur of the Year. In 2002, the National Business Aviation Association awarded him its Lifetime Achievement Award for Meritorious Service to Aviation. In May 2005, he received Purdue University’s highest recognition to engineers, an honorary doctorate in engineering.
Recently, Raisbeck was the recipient of the prestigious Pathfinder Award, bestowed by Seattle’s Museum of Flight in October 2007. The award honors individuals from the Pacific Northwest who have significantly contributed to aeronautics and astronautics.
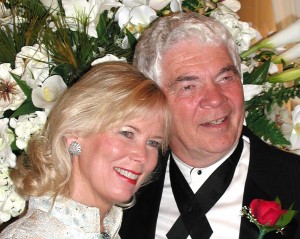
James & Sherry Raisbeck have donated generously through their foundation, benefiting Purdue University, the Pacific Northwest Ballet, the Seattle Symphony, the Fred Hutchinson Cancer Research Center, the Cornish College of the Arts & other organizations.
Raisbeck was cited for his numerous contributions to the safety and performance of aircraft and his influence on many business aircraft designs. The award acknowledged a common theme in his contributions that sums up his life’s work: a unique ability to approach aeronautical problems with multidimensional solutions.
Karen Di Piazza co-authored this article. Additional information was incorporated from an article written by Kim Blonigen, published in King Air magazine in October 2007.