By Di Freeze
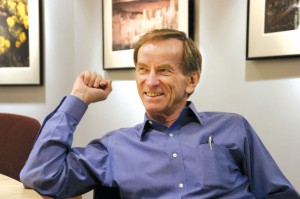
General Atomics Vice Chairman Linden Blue talks about the latest innovations at GA, as well as past adventures, while on a recent visit to Denver jetCenter at Centennial Airport.
Linden Blue has always been very interested in technology. That interest has led him from innovating Learjet product improvements while executive VP and general manager of Gates Learjet in the mid-seventies, to overseeing the development of the Lear Fan in the early eighties and the Beech Starship in the mid-eighties, and more recently to involvement in the development of unmanned aerial vehicles and nuclear reactors.
Throughout his entire career, the present vice chairman of General Atomics has remained involved in aviation, in one form or another. His interest began when he was about 8. Blue was born in Meeker, Colo., but moved to Denver when he was three. He always returned to Meeker for part of the summer.
“Shortly after the end of World War II, the city fathers of Meeker decided they needed an airport. My grandfather was a member of the Lions Club; they took on the project of clearing a mesa right outside of the city for the first airport in Meeker,” he said. Blue’s interest in aviation intensified “with the clearing of the sagebrush.”
“And then one day, suddenly, an airplane landed there,” he said. “I was born in 1936, so I was in a very formative age during WWII. There was a lot of romance in the air, all these fighters and bombers, and the air factor was very important in winning that war. I figured out at an early stage that if you had to have wars, it was better to be in an airplane than down slugging it out in the trenches.”
Blue and his brother, Neal, who was a year older, graduated from Denver’s East High. Both brothers went on to Yale, and decided to look at business opportunities on the economic frontier, which at that time seemed to be in Latin America.
“Central America and South America,” Blue said. “At that time, you couldn’t drive around Latin America. We hatched this plan to learn to fly so we could go into business somewhere in Latin American after we graduated.”
Linden Blue began his flying lessons in 1955, soloing in a J3 Cub that autumn, before moving on to an Aeronca. He clearly remembers his solo.
“I was very anxious to do it,” he said. “I suppose I always had an excess of confidence that I’d not only be able to take off, but also land without breaking anything. It turned out that way. I remember vividly when the guy got out of the airplane and said, ‘Go for it.’ That is a moment of truth. Suddenly, you understand that it’s entirely upon you to get the airplane back, and not forget what you’ve learned. You only solo once; you either do it or you don’t. That’s always an exciting time.”
Blue acquired his private pilot’s license on Dec. 17, 1955.
“I soloed in whatever time the minimum then was; I think it was eight hours,” he said. Then I got my license in the minimum, again, which was 40 hours. When you’re in school and carrying a full academic load, it’s a little tough.”
The day after he got his license, the brothers took off in the Yale Aviation Club airplane to fly to Denver.
“That was at Christmas time, in the middle of the winter,” Blue said. “It took four days. In those airplanes, you’re making maybe 80 knots. You look down, and if you have a headwind, the cars are going faster than you are. That’s a long flight, from New Haven (Conn.) to Denver, considering weather and all.”
He said having the Yale Aviation Club was a great advantage.
“We had an airplane that we could fly very inexpensively,” he said. “Then, at spring break, we bought a Yale Aviation Piper Super Cruiser for the outrageous sum of $1,500, and flew it around the U.S., talking to newspapers, so they would back our Latin America flight, and pay us for writing articles. We talked to the major newspapers at that point in time—the Baltimore Sun, the Washington Star, the New York Times, the Houston Chronicle, the San Diego Union, the Denver Post.”
Most of the papers agreed to take their articles.
“It was a fairly no-risk thing for them,” Blue said. “Most of them ran our articles when we wrote them; a few of them gave us an advance. I think the Denver Post gave us $1,000, which was a lot of money back then.”
The Flying Blue Brothers
For the South American trip, Piper Aircraft loaned the Blue brothers a PA-22 Tri-Pacer.
“The idea was to see as much of Latin America as we could in a summer vacation,” said Blue, who was 19 at the time. “We were both in Air Force ROTC, and Neal had summer camp, so we couldn’t take off until he was through.”
A friend, Peter Gillingham, had planned to go with them, but the Tri-Pacer wasn’t large enough, so, instead, he ended up managing the “syndicate.”
“We’d send the film and copy back to him and then he would distribute it to the newspapers,” said Blue.
Linden Blue departed from Combs Aircraft on Denver’s Stapleton Field and picked Neal Blue up in Waco, Texas.
“We headed south, down the east coast of Mexico, and then down through Central America, the west coast of South America, and across the Andes, nine times,” Blue said. “The mountains go up to 23,000 feet. Of course, we couldn’t get to 23,000 feet in a Tri-Pacer, but we went over a lot of passes. That can be a little challenging.”
Blue, who left the U.S. with about 80 hours, admitted that he couldn’t have made the trip without mountain flying training.
“There were two critical factors there,” he said. “One was an old friend who was the first manager of the Meeker airport. I had the benefit of flying with him in the mountains, in his 85-horsepower Taylorcraft—a grossly underpowered airplane. If it’s an 85-horsepower engine at sea level, probably we were down around 60 hp out of Meeker in the summer. He taught me to fly the air currents in that ‘powered glider.'”
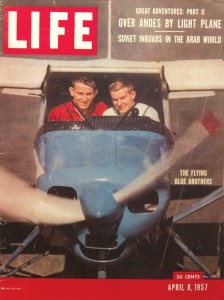
After Yale students Neal and Linden Blue decided to fly around Latin America looking for business opportunities, various publications, including LIFE magazine, bought their story, dubbing them the “Flying Blue Brothers.”
The other factor was Harry Combs.
“Harry said, ‘Well, this is the dumbest thing I’ve ever heard of; there are all kind of perils.’ Harry, as you know, was a brilliant and articulate person,” Blue said. “He then proceeded to describe Latin America and the wonders of flying down there, which he’d done a lot of. Of course, it was irresistible when he said, ‘Well, damn it, if you’re gonna do it, I guess the least I can do is try to make it so you’ll survive.’ He insisted that I take a minimum amount of instrument training and paid for it. It was probably because of that training that we lived through it. I had just a little—enough to be able to get out of trouble, but not enough so that I’d get into trouble.”
While in Chile, the Blue brothers were ecstatic to meet skiing icons Billy Kidd and Stein Ericksen.
“Stein had just invented the swan-dive ski somersault,” Blue recalled. “Acrobatics is an everyday occurrence now, but he was the guy who invented it all.”
When the Blues met Kidd at a bar in Santiago, the legendary Olympic skier told them about the great skiing in Portillo, Chile.
“We love skiing, so that was irresistible,” said Blue, who was a competitive ski racer himself. “We didn’t have time to take a train up there, because it would have taken a day or two.”
When the Blues heard that Lago del Inca (Inca Lake), at 10,000 feet, was frozen (with ice about 18 inches thick), he reasoned that the lake would be strong enough to support an airplane.
“We decided to go up there and land,” he said. “That wasn’t the smartest thing we’ve ever done. Taking off, it was starting to be spring down there, so there was a fissure in the ice that had opened. We were taxiing out for takeoff and going a little too fast; when the nose gear caught a ridge in the ice, it folded it under, and got the prop. It could have all ended right there, except we were able to repair it.”
In fact, the repairs were done that same day.
“To give you an idea of how simple airplanes were back then, the people who maintained the ski lifts were able to get it put back together in the course of about an afternoon,” he said.
They straightened the prop with the use of a vice.
“There was a little bit of serendipity,” Blue said. “There was a young MIT (Massachusetts Institute of Technology) student down there skiing; when he saw the problem, he came over. We were like, ‘How do you bend metal? Well, you heat it up.’ But he said, ‘No, don’t do that; cold bend it.’ His opinion might not have been right, but at least he knew more than we did, so we bent it in a vice as he supervised. On the Tri-Pacer, the nose gear is supported with tubular steel. The lift operators sleeved and welded it.”
The next morning, when the air was cold and the ice solid, they took off. The Blues traveled from Santiago as far south as Puerto Montt in Chile, before crossing over into Argentina, and heading up the east coast of South America.
The incident at Portillo was just the first problem. They made a forced landing in a suburb of Buenos Aires after their engine quit due to fuel contamination.
“That took some time to repair,” Blue said. “Then, we had another forced landing in the southern part of Brazil. The combination of the two made it necessary for my brother to go back and get a new pair of wings for the airplane. I stayed in Brazil and continued doing the articles and supervising the repair work on the airplane.”
As a result, instead of taking two months, which would have gotten Blue back in time for the start of school, he was over a month late getting back.
“I had to take a reduced load that semester and then pick it up the rest of my time in college,” he said. “Neal went back to school. He was going into his senior year; I was going into my junior, so it was more important that he be there. Once we got all the repairs made, Neal flew back and joined me in Rio, and then we flew back the rest of the way.”
The brothers flew up Brazil, across part of the Amazon basin, and up through the Caribbean, island hopping.
“I think we traveled a total of 22,000 miles, which is roughly the distance around the world,” Blue said. “We logged over 200 hours. We met wonderful people all throughout Latin America in the process. There’s a fraternity in aviation. Particularly at that point in time it was unusual to see a little airplane, and one with a U.S. registry. People would come up and introduce themselves and ask, ‘Who are you and what are you doing?’ It was a fabulous trip.”
He adds that it was the sort of thing he’d never want his own children to do.
“Fortunately, we survived it,” he said. “Once you have that kind of experience, it does give you confidence that maybe you can do almost anything you want. It was a great learning experience. For that, I give my parents great credit because once we had the problems that we had, they didn’t insist that we give up. They understood that we had to go through it and persevere, drive it to its conclusion.”
Because of the problems they encountered, the trip ended up costing a lot more money than they expected.
“The various newspaper articles paid for a lot of our expenses, but the thing that got us out of hock was selling the article to LIFE magazine,” Blue said.
Their story made the front page of LIFE on April 8, 1957. The article was entitled “The Flying Blue Brothers.”
“I think we got $8,000 for it,” Blue said. “That was a huge sum for that time, particularly for college kids.”
Chocolate and bananas in Nicaragua
The following summer, after Neal Blue’s graduation, the brothers narrowed down their interest to Central America.
“We sold the Super Cruiser and bought a Stinson Voyager,” Blue said. “I think we paid $2,000. Compared to the Super Cruiser, that was a pretty good airplane. We flew that around Central America, just focusing on business opportunities there and in Nicaragua.”
Following that trip, they decided to start a banana and cacao (the source of cocoa and chocolate) plantation in Nicaragua. They decided on that venture as a way to make their fortune initially because of a man they met the previous summer, while flying around Guatemala.
“One of the guys who saw our airplane land in Guatemala City was Bill Paddock, a PhD in agriculture from Iowa State University,” Blue said. “I think he was head of the Point Four program, which was an agricultural extension program of the U.S. Government. He told us there was a great opportunity to grow cacao. Based on that, the next summer we came back and revisited Bill and his wife Liz, and looked at specific opportunities for growing cacao throughout Central America, Nicaragua, El Salvador and Guatemala.”
Larry Ulrich, an old friend who helped the Blues acquire and develop the Denver jetCenter and Rocky Mountain jetCenter Network of FBOs, says their agricultural idea was revolutionary at the time.
“They theorized that the cacao would thrive in the shade of the banana tree,” he said. “They were some of the first people to grow the combination of the two.”
Although the products were symbiotic, the Blues did end up with a problem.
“The bananas got Panama Disease, before we could get the first crop out,” Blue said. “We were in a world of hurt. Necessity is the mother of invention, as they say. Bananas were dying, and there’s no cure for Panama Disease. We talked to agronomists and were told that there was a disease-resistant variety that had been developed up in Honduras. We engineered a way to import them to Nicaragua.
“That has now become the economic salvation of the Caribbean coast of Nicaragua. So, the enterprise was a success, but it was never profitable for us. We got nothing out of it, except the satisfaction of knowing that our efforts made a major economic impact on the Caribbean coast of Nicaragua. At least it was a great experience.”
During that period, the Blue brothers, now flying a single-engine Cessna 170 around, started to become a little nervous. While in Denver, Linden Blue went to Combs Aircraft to take a demonstration ride with Ulrich, who was selling airplanes there at the time. He chose to try out a twin-engine Piper Apache.
“We took off from Stapleton in the evening,” Ulrich recalled. “We had no sooner got the landing gear up when one of the engines failed. I was horrified. When you’re trying to sell someone an airplane, it’s the wrong time for an engine to quit!
“We got back around and landed safely, and when we got our wits together, I said to Linden, ‘Well, I guess that’s the end of that. You’re not going to be interested in buying that airplane, are you?’ He said, ‘Are you kidding? If the engine had quit on the 170, where do you think we’d be right now? We’ll take it.'”
Blue said that part of the reason he was interested in buying a twin-engine aircraft was because he’d already seen an engine fail at “a very bad time.” It was while flying the Stinson over the jungles of Honduras.
“Suddenly we noticed that we were leaving a big cloud of black smoke,” Blue said. “Fortunately, we limped in and landed on a small strip in British Honduras. It turned out that the oil radiator had failed and we’d lost all our oil; the plume of black smoke was oil spraying on the manifold and burning. … We took the oil radiator off, put in a piece of oil tubing and pressure hose from a Caterpillar tractor, and flew the airplane all the way back to the U.S. … That’s why I believe in twin-engine airplanes today.”
Blue had another hair-raising incident in 1961, while returning from the U.S., after purchasing equipment for the farm in Nicaragua.
“Cuba lies east and west, across all the thresholds to Latin America,” he said. “It’s 600 miles long. If you go around Cuba, it’s a long way around, either way you go, so there’s a great desire to fly over Cuba. There’s an international airway, so I filed for and got an instrument flight plan to fly over Cuba on my way to Nicaragua. As I was approaching the north coast of Cuba, the Cubans revoked my clearance, and told me to land in Havana.
“I said, ‘No, I’ll go back to Key West.’ They sent fighters to intercept me and make sure I landed in Cuba, which I did. I ended up in jail for 12 days. Anybody can go through 12 days, but it was an intense period, because that was right before the Bay of Pigs invasion. If I hadn’t gotten out when I did, I probably would never have gotten out.”
He got out 13 days before the invasion, and later learned that all of his cellmates were executed the morning of the invasion. He said it was probably 10 days after he got out that they learned that the invasion was coming from Nicaragua.
“They wouldn’t have let me out, once they learned that it was coming from there, because they were very suspicious of my connection with Nicaragua in the first place,” he said.
After flying the Apache for a couple of years, Blue upgraded to a Beechcraft Twin Bonanza. He said that being in business in Latin America continued to make flying essential.
“There were no roads,” he said. “If you wanted to make a development in the hinterland, you pretty much had to fly. There was enormous synergy between what we wanted to do from a business standpoint, and the fact that we could fly in and have the mobility of flying. We couldn’t have developed our agricultural business in Nicaragua without aviation.”
No more waiting
Toward the end of 1961, the military grew tired of waiting for Neal and Linden Blue.
“We had gotten our commissions in the Air Force, but both of us had been on essential industry deferments,” Blue said. “Eventually, the patience of the Air Force ran out, and they ordered us to active duty.”
Linden Blue entered the Strategic Air Command and Neal Blue the Air Transport Command. When that happened, the Nicaraguan Development Bank, which had done the financing, took over the plantation.
“We were no longer able to protect our interests there, which isn’t to say it was unreasonable, because we couldn’t be there and couldn’t make it work,” Blue said. “They were within their rights to do that.”
Linden Blue entered service about six months before his brother, and served in SAC for three years. Although he wanted to fly, his job was security officer.
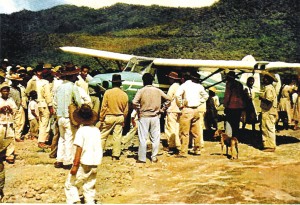
After “Blue Bird” landed on a plateau in the mountains of southern Mexico, Totontepec villagers clustered around the aircraft. On takeoff, the runway was so short that the plane had to drop off the edge of the plateau.
“I had originally taken Air Force ROTC because I wanted to fly, but they changed the rules midstream,” he said. “They said, ‘If you’re going to fly, you have to sign up for five years.’ I didn’t want to do that.”
While Linden Blue was stationed at Lowry, in Denver, Neal Blue was stationed in Europe and Dayton, Ohio. He developed contacts there that allowed the brothers to get into the commercial real estate business in Denver once they were out of the military.
Going into real estate wasn’t totally alien for the brothers. Their parents owned Blue and Blue Realtor in Denver.
“They were in residential real estate,” Blue said. They soon began branching out, through Cordillera Corp.
“It started with real estate, and then we got into construction, and then ranching and some natural resources—oil and gas,” Blue said. The brothers continued that way for over 10 years. Blue said that although flying was less important in Colorado than it had been in Nicaragua, aviation was important in some of the ranching and real estate activities.
“It was always very helpful to be able to fly around Colorado or around the West,” he said.
Ten years after his flight to South America, Blue and Greg Austin, a friend in Denver, bought a Piper Twin Comanche, and flew a similar flight.
“That airplane was suitable to those altitudes,” he said. “It was turbo supercharged, so it could fly to 22,000 feet. We could look down on Mount Aconcagua, instead of looking way, way up at it.”
During that period, Blue also got into the political arena. He was elected councilman at large for the City of Denver, and served in that position for four years. At the end of his term, he attended Harvard Business School.
“I was considering whether I would want to go further in politics—maybe run for mayor of Denver,” he said. “I figured that if I did that, I should be at least a little bit prepared.”
But after completing a 13-week advanced management program at Harvard, Blue decided he’d rather be in business.
The Lear Fan and the Starship
The end of his political career seemed like a good time for a career change.
“I decided that I would like to really indulge my great interest in aviation,” Blue said. “I very much admired Harry Combs, who at that time was president of Gates Learjet. I thought that aviation manufacturing was an ideal career and that it would really be great to work for a company like Gates Learjet, and Harry.”
When he expressed his interest to Combs in 1975, he was quickly hired.
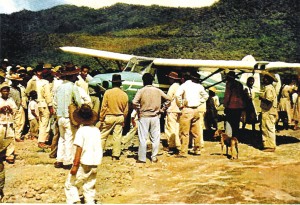
After “Blue Bird” landed on a plateau in the mountains of southern Mexico, Totontepec villagers clustered around the aircraft. On takeoff, the runway was so short that the plane had to drop off the edge of the plateau.
“I went to Learjet as assistant to Harry Combs, in charge of strategic planning,” he said. He went from heading strategic planning to serving as executive vice president and general manager of the aircraft division and later the avionics division as well. He remained with the company through 1980.
“That was a period of huge expansion,” Ulrich said. “Linden presided over, among other things, the design and opening of Lear’s Tucson facility, which was a huge maintenance and completion center.”
Blue was one person who influenced Gates Learjet early on to be more aggressive in product development and to create higher performance aircraft through aerodynamics. His association with Richard Whitcomb of NASA was a huge benefit.
“Whitcomb developed what we now know as winglets,” Blue said. “The Arab oil embargo had happened, and cost of fuel had gone up. I felt it was important not only to have superior performance in airplanes, but also fuel economy. I thought that the days of the Lear 20 series—24s and 25s, with the turbojet engines—were numbered, and that we should focus on a more economical fanjet airplane, using either the down-rated 731-1 engine or a JD 15D.”
He explained that the only way to make a Learjet do that was to get rid of the weight of the tip tanks and add a little more wing.
“You can’t add a lot more wing without getting wing bending, but if you use winglets instead, you can reduce wing bending and avoid changing the structure too much,” he said. “You see winglets everywhere now, but Gates Learjet was the first company to put winglets on a business jet. We did it in great secrecy. We painted the winglets black, so nobody could see them. And then we put what looked like big bass fiddle cases on them.
“We were operating out of the Wichita airport, and Cessna was right across the field. We didn’t want Cessna to know what we were doing, so we’d taxi out with these big things on. We figured if they saw them, they’d assume they were some sort of exotic antenna deal. Then, just before takeoff, we’d remove these shrouds, and quickly take off, so nobody would see them.”
Blue said they completely surprised the industry when they revealed the winglets.
“The extra performance you got by the winglets was dramatic,” he said. “That allowed us to fly efficiently at 51,000 feet.”
The first Lears to utilize the winglets were the 28s and 29s.
“They were the GE-powered aircraft,” Blue said. “They led the way to the Lear 31 and 55. The reason for all that was to put some vigor into the Learjet line, which it needed by that time. We used advanced aerodynamics to do so. All the Learjets now have winglets, as do all the Bombardier airplanes, Gulfstreams, and many commercial airliners.”
Blue also started fledgling advanced composites activity at Gates Learjet, and extended that to the Lear Fan 2100.
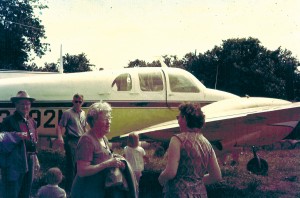
Linden Blue with his grandparents in Nicaragua (circa 1960) where he and his brother Neal grew bananas and cacao.
“I saw what you could do with advanced composites, and became convinced that advanced composites were the way of the future for aviation,” he said. To this day, Blue believes that all airplanes will one day be made of advanced composites, because of the strength, characteristics, and advantages such as their light weight as well as lack of corrosion or fatigue.
“Still, there are manufacturing problems with advanced composites that nobody’s solved yet,” he said. “Weight is what aircraft are all about. If you can make a lighter airplane, you have a huge advantage. I thought composites had great potential for reducing weight.”
Blue said the Lear Fan started to come on stream at the time that the industry turned south in 1979.
“So there were financial problems,” he said. “The market was starting to go away, and they needed more capital. I came to a parting of the ways with Lear Fan and went to Beech.”
By that time, Blue had become a recognized expert in composites technology. Beech was also convinced that composites were the way to go.
“Beech made a major bet on that technology,” Blue said. He started out at Beech as president and CEO, and remained there for two years. During that time, he became a director of the Raytheon Company.
“The thing that’s always turned me on in aviation is the innovation part of it,” Blue said. “I’ve never been interested in being a caretaker manager. If you could dramatically improve the technology, that interested me. That’s what I want to do. There was great potential for that at Beech.”
During his tenure, Beech solidified its position in training airplanes with the T-34C, got heavily into the Beech 1900 series, and started the Starship, which became the foundation for Raytheon/Beechcraft’s entire line of current “Next Generation” composite Premier and Horizon business jets.
“We increased the production capability, and got started in the composites business,” he said. Although Blue was pleased that the Starship was an all composite airplane, he knew that the process had to become automated.
“The Lear Fan was substantially a black metal airplane; black composites had been substituted for aluminum,” Blue said. “You really can’t do it that way. Composites require a different approach. I was convinced that filament winding was the key to making composites economical, and that the process had to be automated.”
In the process of starting the Starship, they visited all the composites operations in the U.S., from Boeing on down.
“That further convinced me that filament winding would solve the problems of composites,” Blue said. “We needed to come up with a manufacturing system that was inherently suited for composites, rather than just duplicating aluminum manufacturing processes.”
But Blue’s ideas were a little too advanced for Raytheon.
“I was unwilling to preside over an airplane that was going to be fundamentally flawed,” Blue said. “Because the production process wasn’t automated, I believed it would be too expensive and it would also be much harder to control weight. We had a major disagreement over how the airplane was to be built; I insisted on automated processes. They believed the technologies we had developed were not sufficiently mature. They owned the company and they won the argument. So I left. Interestingly, they’re doing the Premier and Horizon fuselages today very similarly to how we had originally planned to do the Starship.”
Ulrich said that Blue was way ahead of his time in terms of technology, but that he ran into a classic union problem.
“To filament wind an airplane, you have to put it on a spool, if you will,” he said. “You wind the filament around it with a machine. That’s what Linden means by automated. Beech was taking the layers of carbon fiber and laying them on top of each other, and then curing them in an autoclave. It’s very labor intensive, and as he says, it’s much harder to control the weight.
“As Linden correctly predicted, the cost of doing it that way, instead of filament winding, drove the price of the Starship up to the place that it drove it out of the marketplace, and the Starship became way too heavy. Linden could see that, and Raytheon maybe could, but the Beech labor unions were completely opposed to filament winding because it’s an automated process, and that means fewer jobs.”
Blue said, “It was a manufacturing culture clash, more than anything else.” He flew the Starship on it fifth flight, and found it to have terrific characteristics.
“It was a wonderful flying airplane,” he said. “In fact, I rolled it on that flight. That was a lot of fun.”
Blue said that if you’re going to do a new technology, you’d better really understand how to do it.
“I didn’t know everything there was to know about composite manufacturing, but I knew that doing it by hand was not the way to do it—not the way to be successful,” he said. “I knew there were inherent differences with composites.”
Rocky Mountain jetCenter Network
In a few years’ time, Blue would have the opportunity to experiment further with composites. In the meantime, in the mid-1980s, Neal and Linden Blue acquired what’s now the Rocky Mountain jetCenter Network. That network consists of the Salt Lake jetCenter, the Colorado jetCenter in Colorado Springs, the Fort Collins-Loveland jetCenter, and Denver jetCenter at Centennial Airport, which is one of the largest FBO operations in the country and also consistently rated as one of the top rated FBOs in independent pilot surveys. The Blues bought the existing operation as a way to remain involved in aviation, following Linden Blue’s departure from Beech.
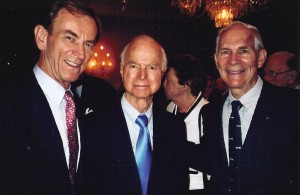
L to R: Linden Blue, former executive vice president and general manager at Gates Learjet, with Charlie Gates and Bob Beery, former head of Learjet flight test.
“These jetCenters were FBOs that Beech had, and they wanted to go in another direction,” Blue said. “I had felt that they should consolidate and vertically integrate, but they wanted to sell them off and we were interested in buying them.”
General Atomics
In the mid-1980s, after being involved in the oil and gas business, the Blue brothers questioned if they should continue to invest in that area.
“At that time, oil and gas assets were fully appreciated; they commanded high prices,” Blue said. “What basic energy source was undervalued? Well, nuclear. That was very interesting to us. And obviously it was easier to buy technology and resources in nuclear because it was so grossly undervalued. It still is.”
That’s why they ended up acquiring General Atomics, a nuclear physics and defense contractor headquartered in San Diego. General Dynamics Corp. founded the nuclear power research company in 1955 to explore the peaceful uses of atomic energy, but sold it to Gulf Corporation 15 years later. Chevron acquired the company in 1984. In 1986, Neal and Linden Blue acquired GA for $50 million.
The Predator
General Atomics Aeronautical Systems, Inc. (GA-ASI), an affiliate of GA, recently merged with General Atomics Reconnaissance Systems to seamlessly integrate aircraft with sensor and weapon systems. Neal Blue is chairman and CEO of the combined enterprise.
GA-ASI has four facilities in Southern California that are dedicated to the design, development and manufacture of unmanned aircraft surveillance systems and associated hardware. A year after acquiring GA, the Blues hired retired Rear Adm. Thomas J. Cassidy Jr., a fighter pilot, to pursue advanced technology projects. In 1991, GA acquired Leading Systems, Inc., a floundering drone business.
“We were fortunate enough to find a company that we could buy inexpensively that made an all-composite, unpiloted airplane that we later developed into the Predator,” Blue said. He said the development of the Predator was an outgrowth of their desire to help their friends in Nicaragua.
“At that time, the Contras were resisting communism and the domination of the Soviet Union, through the Sandinistas in Nicaragua,” he said.
In 1995, GA-ASI, formed in Rancho Bernardo to build UAVs, introduced the Predator, a successor to Amber and Gnat UAVs, originally bought by the U.S. government. Predator aircraft procured by the U.S. Air Force and by the Italian Air Force have accumulated more than 120,000 flight hours.
“The Predator is doing some of the best work in Iraq and Afghanistan, in terms of supporting U.S. troops and also Iraqi troops,” Blue said. “Essentially, everywhere there have been geopolitical problems, Predators have been deployed. They’ve saved lives and kept many U.S. forces out of harm’s way.”
Predator B has a 500 percent greater payload capacity than Predator, an endurance over 30 hours, speeds greater than 220 knots, and can operate above 50,000 feet. The turboprop powered Predator B MQ-9 “Hunter-Killer” is operational with the U.S. Air Force. The I-GNAT-ER is currently operational in combat with the U.S. Army. Warrior, a derivative of the combat-proven Predator, provides long-endurance surveillance, communications relay, and weapons delivery missions, with double the weapons capacity of Predator. Altus and Altair are operated in conjunction with NASA for scientific research, atmospheric monitoring, surveillance and reconnaissance missions.
In early September, GA-ASI was awarded a contract for the first Department of Homeland Security, Customs and Border Protection unmanned aircraft system, which will patrol our nation’s borders. The contract calls for GA to deliver one system, which will initially be comprised of a Predator B aircraft equipped with EO/IR and the Lynx synthetic aperture radar, ground control station, launch and recovery system, support equipment, engineering and logistics support. The off-the-shelf rapid delivery system, which will be operated and maintained by GA-ASI personnel, will provide long-endurance surveillance, as well as communications relay for the CBP mission.
General Atomics’ UAV aircraft and systems can provide 24/7 situation awareness over wide areas with near instantaneous precision strike capability. The Predator can fly for two days without refueling.
“If it weren’t for the light weight of composites, Predator couldn’t do that,” Blue said. He adds that the same can be said for the GlobalFlyer, which, piloted by Steve Fossett, recently completed the fastest, non-stop, non-refueled, solo flight around the world.
“The GlobalFlyer couldn’t have made it, if it were made out of aluminum,” he said. “You couldn’t get it light enough to do it.”
Blue says he admires enormously what Burt Rutan has been able to accomplish. Still, his ideas differ from that of his friend.
“Burt thinks way out of the box on a lot of things,” he said. “Both the SpaceShipOne and the GlobalFlyer were significant accomplishments. Both of them required composites. The big advance with the GlobalFlyer was the composite material; otherwise, it’s just a matter of making it aerodynamically efficient and putting a lot of fuel on board. I think 82 percent of the weight was fuel. But Burt’s interests have always trended toward the one-off technical demonstration type airplanes; I’ve always gone to the manufacturing side, making it feasible economically from the manufacturing standpoint. The challenge is making aircraft economically.”
Even today, the biggest problem Blue sees with composites is in the area of production.
“If you can solve some of the production problems, there remains great opportunity,” he said. “We’ve been making airplanes out of aluminum for 75 years, very effectively. When you look at the history of making airplanes, there have been two ways of doing it, basically. One was the way the Wright brothers did it, out of fabric and tubular steel and wood.
“The second was the way that Douglas did it, with the DC-3. That was a revolution. It was that aluminum material system that allowed the DC-3 to form the foundation of commercial air travel. You can’t very well conceive of a DC-3 or 747 made out of fabric. Aluminum was the technology; that happened 75 years ago. I believe that advanced composites are the next technology that enables a significant aerodynamic improvement. But you can’t do it the same way that you did aluminum. It’s a different kind of material.”
Blue said if you make a lot of small parts, as you do with aluminum, when you put them all together, you don’t get any weight savings.
“You have to look for better ways to do that,” he said. “You have to automate the process to put those pieces together.” The process for aluminum is still very manual and labor intensive.
“In most composite operations, there’s still a lot of hand labor, including the Predator,” Blue said. He said that with advanced composites, the only vulnerability is ultraviolet light.
“It’s very easy to protect it from ultraviolet light by painting it,” he said. “So, you have to paint airplanes made out of composites. It’s no big deal. But you have the huge advantage of no fatigue and no corrosion, low weight and high strength, if you design it right.”
He said that composites are inherently better in every physical sense.
“The challenge is in making composites reasonably economical even though they are inherently better, and more expensive,” he said.
Other GA affiliates
Today, Linden Blue serves as vice chairman and Neal Blue as chairman and CEO of General Atomics, which specializes in diversified research, development and manufacturing in defense, energy and other advanced technology arenas. GA provides information technologies, nuclear technology and instrumentation, aircraft launch and recovery systems, superconducting magnets, systems for hazardous material destruction, magnetic levitation systems, and many other products and services for government and industry.
“There’s been an enormous synergy with all those technologies, in terms of abilities to handle high-temperature materials and high power, so that the nuclear business has spawned a lot of other very interesting technologies,” Blue said.
When the Blues acquired General Atomics, the company employed about 1,500 people, including a high percentage of graduate degrees and PhD’s. Today, they employ about 3,000.
“It’s a technical powerhouse,” Blue said. “It was then and still is, even more so.”
The company’s main facilities in San Diego contain over one million square feet of engineering and test facilities, precision manufacturing installations and advanced technology laboratories. GA and its affiliates also conduct operations from Berlin, Dresden, Moscow, Tokyo, Australia, Washington, D.C., Denver, New Mexico, Oklahoma and Utah.
GA affiliated companies include General Atomics Electronic Systems (GA-ESI), ConverDyn, Cotter Corporation, Heathgate Resources, Nuclear Fuels Corporation, and Rio Grande Resources Corporation. German affiliate Spezialtechnik Dresden GmbH (STD) is engaged in developing industrial realestate as well as in remediation of large-scale uranium and lignite coal mining areas, manufacturing prefabricated concrete components for the construction industry, modernizing and reconstructing light railcars, and reprocessing munitions. Blue said GA is a “treasure trove of technologies.”
“All because of this high-tech foundation of nuclear technologies, both fission and fusion,” he said.
General Atomics’ basic research into fission and fusion has made GA, and its affiliated companies, one of the world’s leading resources for high-technology systems development ranging from the nuclear fuel cycle to remotely operated surveillance aircraft, airborne sensors, and advanced electric, electronic, wireless and laser technologies. GA’s latest technologies include ultra-wide band transmission, advanced landing systems for aircraft carriers, and electromagnetic launchers, which are the next generation of catapults for aircraft carriers.
“That same technology leads to rail guns, which will use electromagnetics instead of chemical propulsion for artillery shells,” Blue said. “This is very interesting to the Navy. That also is the same technology that is leading to viable magnetic levitation transportation systems.”
General Atomics was also one of the early makers of Magnetic Resonance Imaging devices.
“Again, it was all the technical synergy of being able to handle magnetic fields very well, understanding high-power magnetics,” Blue said.
The company had been involved in nuclear reactors since it was founded.
“At that time, Eisenhower conceived of the Atoms for Peace program initiative,” Blue said. “John Jay Hopkins, a visionary, was the chief executive at General Dynamics, which was a technology company at that time. They said they wanted to get into this industry, and they convinced the city fathers of San Diego that they should do this there. They got some land up north of San Diego, which at that time wasn’t worth very much, and founded this company, and this campus of nuclear technology and developments.”
GA has been the primary developer of modular helium-cooled nuclear power reactor systems. Its TRIGA research reactors have operated around the world for over 45 years.
“After a 20-year wait, I think our fundamental belief in the importance of nuclear energy is starting to be recognized, even by the environmentalists, as a superior way of getting energy that is environmentally very desirable, because there are no emissions, essentially, and even less radiation than you get from burning coal,” Blue said. “The technology we have at General Atomics allows you to do it about 50 percent more efficiently than current water reactor technology.”
Blue said meltdown proof nuclear reactors are also on the horizon. The technology ensures safety and no chance for a Chernobyl or a Three Mile Island.
“You can’t have a meltdown,” Blue said. “That’s guaranteed by the laws of physics; it’s physically impossible. Also, our particular technology lends itself to not only creating very little nuclear waste, but also destroying old nuclear waste, so it’s probably the key to solving the nuclear waste problem.
“Nuclear fusion is the ultimate source of power. Fusion is the power of the sun. The problem is making fusion viable with the gravity of the Earth. But we have one of the world’s leading fusion devices at our facility in San Diego, and it’s going to be the model of the international fusion reactor, which is going to be built in France. Fusion provides the potential for essentially unlimited energy, because it’s fueled by deuterium and tritium.”
Blue said there is “literally the promise of unlimited energy for the future, on an economical basis.” He believes the distinguishing feature in all the technologies that GA deals with is that they’re very advanced and very significant in terms of improving the human condition.
“Having unlimited energy allows you to postulate the development of the world where everybody can have housing, everybody can have food, and everybody can have adequate health care and education—a much higher living standard,” he said. “Everybody—not just the wealthy countries of the West. That’s hugely important. And that’s what turns us on about General Atomics. We’re dealing in sciences that are really important to making a better life.”