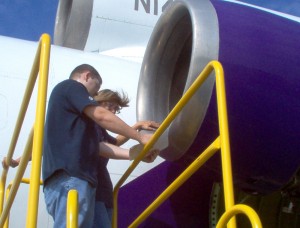
In June 2004, FedEx donated a retired Boeing 727-100 freighter to Guilford Technical Community College. Students receive hands-on experience in the college’s aircraft maintenance technician program.
By Henry M. Holden
The Piedmont Triad, anchored by the cities of Burlington, Greensboro, High Point and Winston-Salem, N.C., is the nation’s 36th largest metropolitan area, with more than 1.5 million people. It has a strong logistics and transportation cluster, including about 18 aviation companies that employ more than 3,200 people, with an average annual wage of $46,000.
The aerospace business is growing in the area. Triad aviation executives feel the industry has climbed out of the hole created by the terrorist attacks of Sept. 11, 2001. That climb began in 2004, and in the past three years, Triad companies have stepped up production, hired new employees and welcomed new neighbors, such as HondaJet and FedEx.
Since 2004, B/E Aerospace has grown in sales from $750 million to over $1.1 billion, and Landmark Aviation has become the world’s largest Beechcraft dealer and Piedmont Aviation Component Services LLC signed a five-year contract to maintain the landing gear for all 737 jets in Delta Air Lines’ fleet. Guilford Technical Community College has been expanding its aircraft maintenance program, and TIMCO Aviation Services Inc. has become one of the Triad’s largest employers, with a workforce of about 1,400.
HondaJet raised the Triad’s aviation profile when it announced in February that it would make Greensboro its corporate headquarters and location of its manufacturing facility. FedEx will grow the Triad’s aviation profile when its mid-Atlantic air cargo-sorting hub opens in early 2009.
Guilford Technical Community College
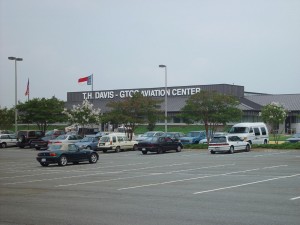
GTCC is going to double its educational space at the T. H. Davis Center. The announcement that HondaJet and FedEx are joining the Piedmont Triad is helping fuel growth in the area.
Guilford Technical Community College, located at Piedmont Triad International Airport (GSO) in Greensboro, is a keystone in the community. It has almost 40,000 square feet of hangar space, classrooms, computer labs and specialty-training shops.
“We’re trying to lure companies to the Triad, and the school is a fairly big part of our pitch,” said Ed Frye, director of GTCC’s aviation program.
The school supplies much of the technical workforce in the area. Its current location, the T. H. Davis Aviation Center, opened in 1989. The center offers an FAA certified, Part 147 airframe and power plant curriculum with associate degree, diploma or certificate options.
“The old freight terminal on the airport was our first location, opened in the 1970s,” said Frye. “We were able to expand, because Tom Davis, the founder of Piedmont Aviation, donated a large sum of money to the aviation center.”
Frye is no stranger to aviation or higher education. He retired from the Air Force after 26 years of flying tankers, helicopters and primary and advanced trainers. He’s been with GTCC for almost 10 years.
“We’re about to break ground on an additional building that will double our square footage,” said Frye. “We started out with plans to build a 20,000-square-foot addition. That is likely to double in size, because of the time that’s passed and the commitments we’ve made to our industry partners. The room will allow us to increase classrooms, laboratories, simulators and computer labs. We expect it to be ready by spring 2009.”
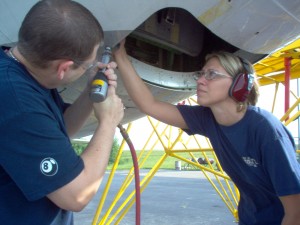
GTCC instructors and technicians are all licensed, with an average of 17 years of industry experience and 10 years teaching experience. Every instructor has a college degree, and many have advanced degrees.
The college also offers opportunities for younger students.
“This fall we’re opening another A&P course directed at high school students,” Frye explained. “It will allow students to come here under the federal government’s Huskins Program. The students don’t pay for school but get college credit. They’ll attend 2.5 hours a day, every day, during their junior and senior years. When they finish, they’ll have completed the airframe requirements for a certificate. Then they have a year to go to complete the power plant requirement.”
The course credits meet graduation requirements for high school electives and apply toward the student’s associate in applied science degree at GTCC.
GTCC’s aviation management and career pilot courses typically have 65 to 75 students enrolled. The aviation systems technology course, which trains A&P technicians, has about 90 students. Both are regular college curriculum programs.
“In addition to that, we run a continuing education program with TIMCO and other Triad companies,” Frye said. “In this program, the intake is about 125 students a year, for four 10-week courses. We have 25 to 30 students in each 10-week course. We teach them to be structures technicians, working largely on sheet metal for the aircraft TIMCO services.”
Embry-Riddle Aeronautical University joined the GTCC campus in 2005. Its first students will graduate this June.
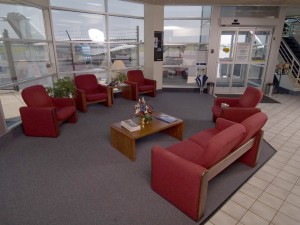
Landmark Aviation customizes and integrates everything from FBO and MRO services to sales, charter and management. The company also offers a turnkey source for all aviation needs, helping to reduce the complexity of aircraft ownership.
“Embry-Riddle operates out of our building and accepts our students who graduate with an associate degree,” said Frye. “It places them in the junior year for a professional aeronautics bachelor’s degree. Students in our town don’t have to leave for Prescott, Ariz., or Daytona Beach, Fla., for the rest of their education. And they pay a reduced rate, because it’s a distance-learning campus.”
Degrees awarded in several disciplines available from ERAU include a bachelor’s degree in professional aeronautics.
GTCC’s aviation systems technology program is the only community college in North Carolina certified to award the airframe, power plant or airframe and power plant ratings. Its licensed capacity is 125 students, based on current space and equipment. Enrollment is currently at 78 students.
“With the recent announcement that HondaJet is making Greensboro its corporate headquarters and manufacturing facility and hiring more than 200 people, we expect to fill any empty seats quickly,” said Frye.
The popular program, certified since 1984, is approaching 1,000 graduates.
“Guilford Tech has graduates who are employees at all the companies on the airport,” said Frye. “We have active partnerships with a few of the bigger companies on the airport as well. We have a lot of people working for TIMCO, Atlantic Aero, Landmark, Tradewinds, FedEx and Comair.
Several graduates have successful careers outside the Triad area.
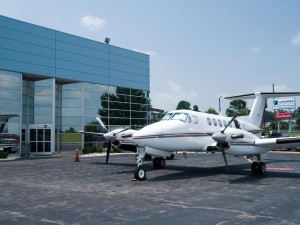
Landmark Aviation is the world’s largest Beechcraft distributor, selling everything from King Airs to Falcon 50EXs. All its sales associates are pilots of the aircraft they sell.
“We have two graduates working on the space shuttle at the Kennedy Space Center,” Frye said. “Another graduate worked for TIMCO and then moved on to the F-22 Raptor program. Our graduates are now teaching at other colleges, and a Northwest Airlines vice president is a graduate of our maintenance program. We have graduates who pilot for major, commuter and regional airlines, as well as the military.”
Books and tuition are reasonable, says Frye, and local companies help with incentives.
“We have academic partnerships with several companies,” said Frye. “If you’re employed with TIMCO for a year, the company will reimburse your tuition, based on your grades.”
Both day and night classes are offered for student convenience.
Landmark Aviation—150 years of aviation experience
Landmark Aviation is one of the oldest continuously operating general aviation companies in the world. It was born out of a 2004 merger between Garrett Aviation, Piedmont Hawthorne and Associated Air Center. The companies had more than 150 combined years of aviation experience.
Garrett Aviation had evolved over its 50-year history from an engine manufacturer into one of the country’s most robust aircraft modification and maintenance services. It brought expertise in airframe, avionics, paint and other modification programs to the merged company.
North Carolina-based Piedmont Hawthorne, one of the nation’s largest networks of fixed base operations, brought 33 owned and managed FBOs to the Landmark deal. Its FBOs are scattered throughout the United States, with three in Canada. It offers service, charter and sales functions.

Landmark Aviation is a leader in business aircraft repair, maintenance and overhaul. It’s the largest supplier of repaired and overhauled TFE731 engines.
Dallas-based Associated Air Center, the third acquisition, is the world’s number-one completion center for the Airbus A320 family of aircraft, commonly known as the Airbus Corporate Jetliner. This combination allows Landmark to offer every service a jet operator may need, including maintenance, repair and overhaul at 19 facilities; aircraft sales; Part 135 charter operations; fueling and ground support services.
Landmark Aviation is doing well, according to Tom Mekis, vice president of aircraft sales, charter and management, who has 10 years with the company.
“We didn’t have a huge downturn after 2001, and we’ve not had a big surge since 2004,” he explained. “We have 295 employees here at the Triad, and it’s been a relatively stable workforce. We don’t overstaff when times are good, so we don’t have layoffs when times aren’t so great.”
The company consolidated departments, bringing jobs to the Triad area.
“We brought in all of the accounting functions that were located across the country,” Mekis said. “We grew the accounting employees to nearly 100 people. Some employees relocated to the Triad, and we staffed some jobs with local people.”
Landmark targets Beechcraft for its aircraft sales.
“Our primary focus is the Beechcraft product line,” said Mekis. “We’re a new Beechcraft dealer for the piston Baron and Bonanza types, as well as the King Air C90 CP. For the last 12 years, we’ve been the number-one dealer in the country for Beech. We’re also the world’s largest Beech dealer in terms of size, number of sales and service centers and revenue generated from new airplane sales.”
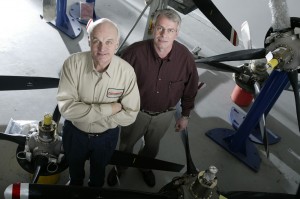
Employees Charles Childress (left) and Sammy Oakley understand the deep customer commitment Piedmont Aviation maintains. ISO will help Piedmont provide even better service to its customers.
Landmark caters to a large part of the East Coast, including New York, Pennsylvania, Maryland, Virginia, West Virginia, North Carolina, South Carolina, Delaware and New Jersey.
We’re a stocking dealer for the King Air C90 CP and the Bonanza,” said Mekis. “We also sell, but don’t stock the King Air 200, the 350, the Premier, Beechjet and the Hawker.”
Landmark Aviation also has a robust pre-owned aircraft sales department.
“We send our sales people around the world to buy inventory,” said Mekis. “Our basic focus is the King Air, Premier and Beechjet, but we’ve sold Cessna Citations, Learjets and others.”
Landmark has two aircraft service facilities and offers charter service.
“We have 31 airplanes on the certificate,” said Mekis. “We’re in the process of adding another three in the next month or so. Most are on the East Coast, with about 10 in the Triad area.”
Landmark also provides a turnkey aircraft management department for aircraft owners.
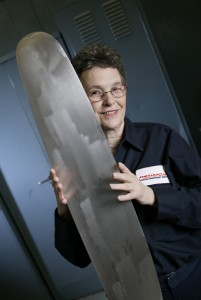
Piedmont employee Sylvia Armstrong brings experience to her job as well as an attention to detail. With a customer base encompassing all segments of aviation, Piedmont provides component repair and overhaul services to clients around the globe.
“We give owners a way to avoid writing 14 checks a month to various companies, for accounting, maintenance, crew and so forth,” Mekis said. “We tailor the process for each owner. Most people want us to consolidate all of their bills into one place. They don’t want to deal with a hangar bill, a credit card bill, a fuel bill and a salary check. The list goes on and on.”
Mekis believes Landmark will be a long-term Triad resident.
“We’re proud to be a part of the Triad community,” he said. “The community has been very good to us. Our roots are here; the majority of our people are local, and that’s probably why our employee base is stable. The Triad has a strong aviation base, and we get most of our technicians from the local colleges. The area has many advantages.”
Piedmont Aviation Component Services—deep roots in the Triad
Piedmont Aviation Component Services, LLC, is one of the largest, most extensively equipped independent maintenance facilities in the world. The company has earned an international reputation in all of its core businesses: propeller and landing gear overhaul and repair, auxiliary power unit overhaul and related parts sales and distribution.
Although the business identity is only about five years old, the company’s roots extend back to the early days of Piedmont Airlines. Tom Davis, who formed Piedmont Airlines, started Piedmont Aviation.
Piedmont Aviation is a Federal Aviation Administration and European Aviation Safety Agency Part 145 repair station, with nearly 65 years of experience in propeller and landing gear overhauls and more than 20 years of experience in auxiliary power units and related component overhauls.
“The company started out repairing and maintaining DC-3s for Piedmont and other airlines,” said Barry Orrell, vice president of material services, who has been with the company 22 years. “Today, we’re a maintenance, repair and overhaul provider for APUs, for commercial, regional and military applications. We also service landing gear and propellers for private, corporate, military and regional aircraft.”
Piedmont Aviation Component Services started in November 2002 when Tom Ferrell and friends Claude Buller and Paul Hilliard acquired the maintenance shop and aircraft overhaul operations of Piedmont Hawthorne Aviation, Inc. It started with 94 employees and only a handful of customers. Today, it boasts 115 employees in two locations.
The corporate office and 56,000-square-foot APU and landing gear shops are located in Kernersville, N.C. The propeller and material services departments are located at Smith Reynolds Airport (INT) in Winston-Salem. The company has regional sales representatives worldwide.
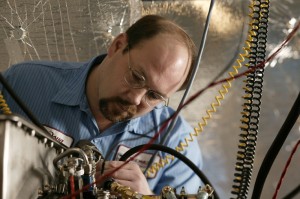
Technician Doug James has the latest technological equipment for use during the repair and manufacturing of APU, propeller and landing gear components. Equally important for Piedmont is having well-trained, experienced personnel.
With just 18 months in business, Piedmont Aviation Component Services had more than $25 million in annual sales.
“In 2006, we topped $45 million in annual sales,” said Orrell. “We’re projecting more positive growth in 2007. We don’t think we’ve reached the full potential of our niche market, and we see even more opportunities in the aviation market. The main driver for us is the commercial airlines; they’ve outsourced a lot of what they used to do to smaller shops, which are now more efficient than what they were in the past. The airlines have reduced their overhead, and that’s fueling the growth in our MRO shop.”
Fueling some of that growth was adding ATR and Canadair Regional Jet landing gear to its list of capabilities in 2004. Piedmont also landed a five-year contract with Delta Airlines to handle work on the GTCP85-129 series APU maintenance support for its Boeing 737-200/300 fleet. These contracts allowed Piedmont to service additional equipment for its current customers, as well as expand its customer base to users of the CRJ, Dash 8-300 series, Jetstream and ATR used by freight companies like FedEx.
“We believe our strongest asset is the experience and dedication of our employees,” said Orrell. “The same customer service ethic that began with Tom Davis is instilled in all our employees today. We have employees that have been with us 40 years.”
The aviation community in the Triad is close-knit.
“Many of our employees had their training at Guilford Tech,” said Orrell.
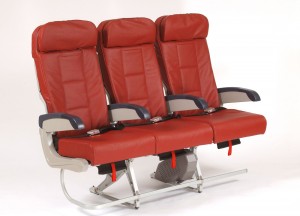
B/E Aerospace designs seats with comfort in mind. More than 6,000 frequent flyers rated the B/E long-haul main cabin seats as the most comfortable on the market.
In June 2005, Piedmont Aviation announced that it had met the rigid standards and requirements of the International Standards Organization 9001:2000 quality certification process, based on eight quality management principles: customer focus, leadership, involvement, problem solving, improvement, decision making and supplier relationships.
“ISO will help Piedmont provide even better service to its customers,” said Bob East, project manager and ISO administrator. “The certification is a badge of honor that shows our commitment to quality and customer satisfaction. Being ISO certified will help attract new customers.”
ISO training inspired employee suggestions that have helped the company save time, lower costs and significantly improve both internal and external communication.
“ISO opened our eyes, offering better ways to measure warranty, improve inventory planning, streamline production planning and smooth integration between departments at our two locations,” said East. “It renewed attention to detail, allowed better control of the thousands of pieces of documentation and has proven to be an excellent extension of the controls required by the FAA.”
B/E Aerospace makes your flight comfortable
With more than $1.1 billion in sales last year, B/E Aerospace has a wide international customer base. The company is the world’s largest manufacturer of cabin interior products for commercial aircraft and business jets. B/E Aerospace also converts passenger aircraft to freighter use and is a leading aftermarket distributor of aerospace fasteners. Its corporate headquarters is located in Wellington, Fla., but many of the executive functions are in Winston-Salem.
B/E Aerospace was organized as a corporation in 1987, and after a number of acquisitions, it significantly expanded the size, scope and nature of the business. Between 1989 and 2001, it completed 22 acquisitions, for an aggregate purchase price of about $1 billion. In addition, it consolidated three major facilities and product lines, eliminating 22 facilities.
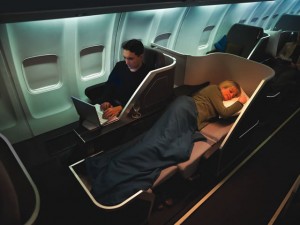
B/E Aerospace’s seating products encompass the entire spectrum of seating available for commercial aircraft. This seat is an ergonomically advanced Lie-Flat POD.
“The Triad area was the beneficiary of some of the planned consolidation we did in 2002 and 2003,” said Michael Baughan, president and COO of B/E Aerospace. “We had to rationalize our business model in the post 9/11 period.”
B/E Aerospace sells its manufactured products to all of the world’s major airlines and airframe manufacturers and to a wide variety of general aviation customers. Its business jet and GA interior products include an extensive line of executive aircraft seats, direct and indirect overhead lighting systems, oxygen delivery systems plus high-end furniture and cabinetry.
Like many of the aviation companies in the Triad, B/E Aerospace began to pull out of the economic downturn in 2004. That year, some projected the company would grow to as much as $750 million in sales.
“The market has continued to grow and expand,” said Baughan. “We’re in a very dynamic market environment right now, and the market for airline cabin interiors is very robust. Our business is heavily oriented toward international carriers based in Asia and the Middle East, and to parts of Europe. The international market continues to be very strong because of the strong financial health and growth of these carriers.”
Until recently, the U.S. airlines hadn’t expanded or modified their jet fleets since before 9/11.
“The U.S. airline industry is in recovery,” said Baughan. “It’s starting to buy new airplanes and invest in new interiors.”
North American carriers are experiencing growth, but other parts of the world have seen significant expansion.
“Major international carriers, which are very profitable and well financed, are flying the transpacific, transatlantic and Middle East routes,” he explained. “They’ve been investing significant sums in new airplanes and for updated interiors for old airplanes. The global airline industry has been buying record numbers of new aircraft; we have to outfit those aircraft. We’re also seeing a noticeable strengthening in the domestic market.”
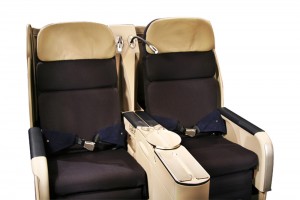
B/E Aerospace has installed more than one million seats. The company has the capacity to produce more than 200,000 seats per year, which is more than 50 percent of the world’s total annual requirements.
Although B/E is a global company, it has a deep footprint in the Piedmont Triad area.
“We have more than 700 employees in the Winston-Salem area,” said Baughan. “Using 2004 as a reference point, we’ve added about 300 people.”
B/E’s employees have a variety of talents.
“We do design, engineering, certification, program management and product development for all of our seating products,” Baughan said. “One of our 14 manufacturing facilities is in Winston-Salem, and it’s also one of our largest facilities. We support our North American and some of our Asian customers from this facility with aftermarket parts. We manufacture a lot of that right here.”
Baughan is proud of B/E’s commercial aircraft cabin interiors.
“People who are relaxed and comfortable on aircraft are probably sitting on our products,” said Baughan. He added, tongue-in-cheek, “If they’re not comfortable, it’s probably our competitors’ products.”
TIMCO Keeps Them Flying
TIMCO Aviation Services Inc., in Greensboro, is the largest independent aircraft maintenance, repair and overhaul provider in the U.S. and the second largest in the world. In addition to its core business of overhauling large commercial transport aircraft, the company provides aircraft engine and component repair and overhaul.
The company also recently created a subsidiary airline/aircraft engineering and modification company, now branded as TIMCO Aerosystems. This new company employees more than 120 engineering personal in the Triad and has satellite offices in Seattle, Atlanta, and Burbank, Calif.
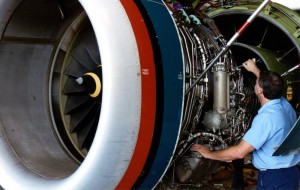
TIMCO operates under FAA approved FAR 145 aircraft repair station certification, which permits a full range of aircraft repair services for nearly all Boeing and Airbus transport aircraft.
TIMCO began operations in 1990 as a dedicated, full-service, state-of-the-art aircraft maintenance facility, housed in one hangar. Today, TIMCO offers its customers 29 hangar bays for aircraft maintenance and modification.
Early on, TIMCO signed a contract with Airborne Express, when the operator was expanding its fleet with the DC-8 operations. Between 1991 and 1992, TIMCO expanded into aircraft composite manufacturing, which remains a core part of the business today, serving airlines around the world with manufactured aircraft interior architectural equipment.
Several years ago, TIMCO acquired Aero Corp, an aircraft maintenance company with facilities in Lake City, Fla., and Macon, Ga. TIMCO continued its steady growth by adding a Pratt & Whitney JT8D engine shop in Oscoda, Mich. Its Greensboro and Lake City operations are the two largest, each at 600,000 square feet. TIMCO also provides services to a number of airlines at six airport line station locations throughout the U.S.
With nearly 3,000 employees, TIMCO provides aviation services at 14 locations across nine states. TIMCO is one of the Triad’s largest employers, with a workforce of about 1,400. It also leases out about 124,000 square feet of hangar space at Smith Reynolds Airport.
“Although we can service a wide range of commercial transport aircraft, what we choose to service is a smaller group based on market demands, such as the Boeing 767, 757 and Airbus types,” said Ron Utecht, TIMCO’s president and COO.
Utecht joined TIMCO in late 2005, after a 39-year career with United Airlines, where he retired as senior vice president of maintenance operations.
After 9/11, TIMCO, along with many other Triad companies, went through a profound downturn.
“We’ve had our ups and downs since that tragic day, but I’m pleased to say that our business is well on the mend,” said Utecht. We fully expect this year to be an upscale year.”
The 9/11 tragedy brought upheaval to aerospace employees as well.
“Some who lost their jobs at airlines joined our company in the Triad,” Utecht explained. “Others returned to their hometowns and, in some cases, to their families left behind. This has contributed to our employee situation over the past couple of years. I’m happy to say that has settled down and we’re enjoying a stability now that is good for our customers, our employees and the community.”
TIMCO is looking for qualified aviation maintenance technicians
“This is a big challenge for us,” Utecht said. “Military talent is an excellent resource for TIMCO, but overall, the supply of qualified personnel is among our most serious concerns.”
TIMCO has developed a strong partnership with Guilford Technical Community College. In addition to the licensed aviation mechanics it graduates each year, GTCC has worked to develop an entry-level mechanic program.
“We have a vested interest in the success of these students, so TIMCO pays the tuition and fees,” said Utecht. “The instructors are experienced mechanics straight from our hangar floor.”
Utecht is hoping for a strong talent pool.
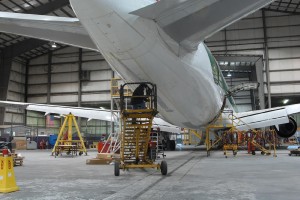
TIMCO recently began offering scheduled line maintenance services at a number of airports in North America. Aircraft overhaul services generate about 80 percent of the company’s sales.
“The way the aircraft engineering and maintenance market is growing, we realize that ‘home-growing’ a significant supply of talent will give us the quality and stability needed to help our business thrive,” he said. “This is why we’re working to create scholarship opportunities for local people interested in attending GTCC’s two-year aviation maintenance program.”
Utrecht sees the community responding to create the right environment to support the development of the industry, in an increasingly competitive environment.
“The aerospace sector holds a lot of promise for the Triad and it needs the community’s full support to remain an important part of the area’s growing economy,” Utecht said. “TIMCO is pleased to have been the founding member of this part of the Triad economic and employment base.”
For more information on Triad companies, visit the following websites: Guilford Technical Community College at [http://www.gtcc.cc.nc.us], Landmark Aviation at [http://www.landmarkaviation.com], Piedmont Aviation Component Service at [http://www.piedmontaviation.com] and TIMCO Aviation Services at [http://www.timco.aero].